Frictional Welding in Manufacturing
by Mashum Mollah Small Business 31 July 2018
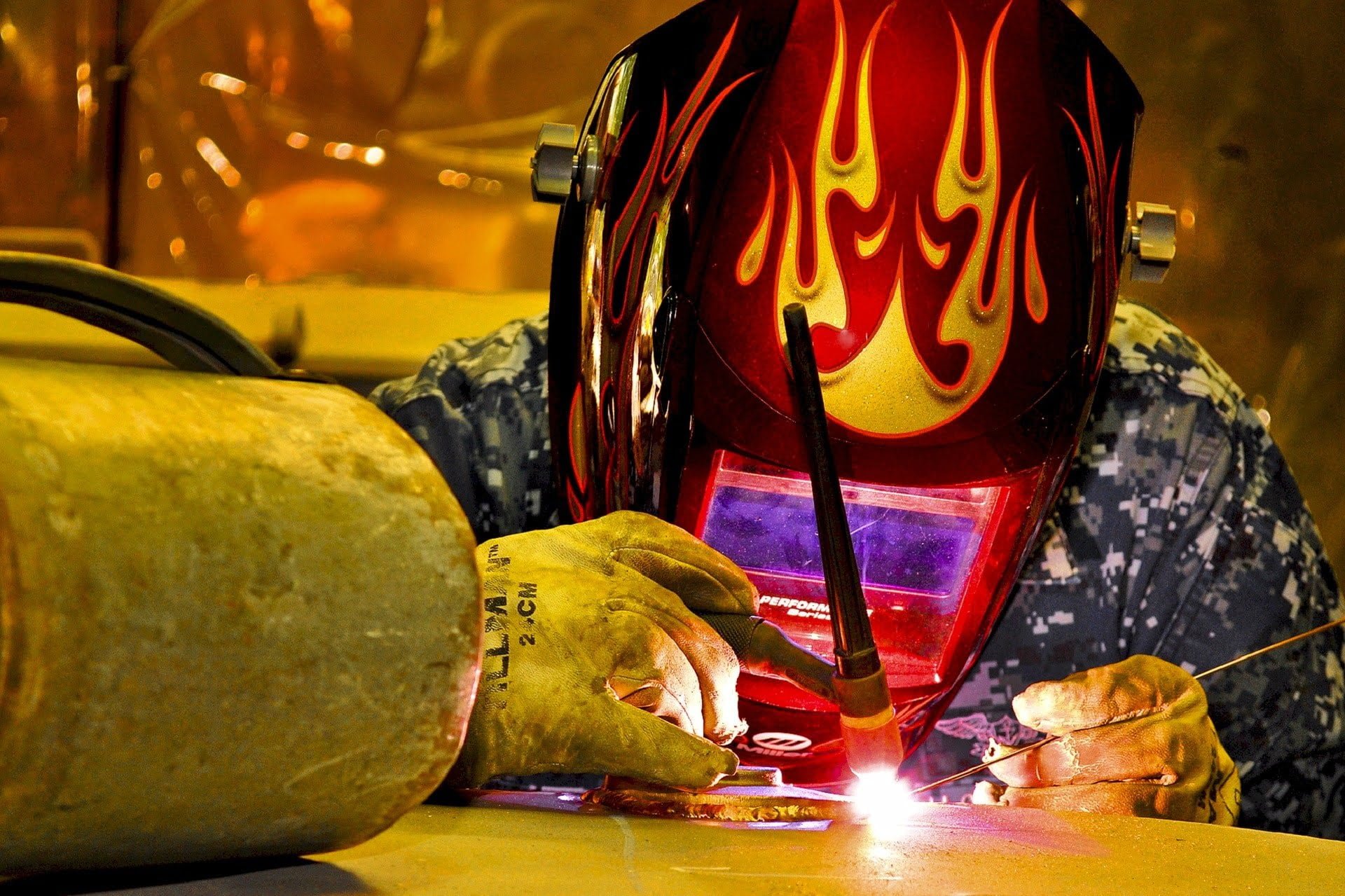
Welding is a necessary process when manufacturing anything in metal or thermoplastic beyond simple forms that are easily cut and shaped. Welding is the process of joining two metal parts together to form a whole piece. In standard welding, external heat is applied to the joint and filler applied to cause the two pieces to form a joint. Depending on the type of weld used, the joint is often stronger than the base material.
Of course, humans can only weld so fast; even the best welders in the country would be hard-pressed to keep up with the demand and flow of an average manufactory. Thankfully, the 21st century has brought about a ton of technological optimizations that allows a company to maximize productivity. These range from computer controlled CNC to welding robots. Utilizing machines to perform the actual welds means that every weld will be nearly exactly the same. One of the most commonly used types of welding in manufacturing is frictional welding, where the heat to create the weld is generated from two items rubbing against each other. Here are four types of frictional welding that are commonly used in factories today.
1. Friction Stir Welding (FSW) :
Essentially, a Megastir friction stir welding machine is able to join together two pieces that lay on the same plane without an outside heat source. That is, the two pieces cannot form an angle. To join the two pieces, a non-consumable tool is spun so rapidly that it causes the metal pieces to where it touches. As the pieces heat, the spinning tool stirs the plasticized metal, causing them to mix, creating the weld. Additional pressure is applied by the tool to seal the weld.
2. Direct Drive Friction Welding :
Using a motor that is directly attached to a shaft, one piece is rotated while the other is held stationary. The two pieces are slowly pressed together and the spinning piece is slowed down at a specific rate. The heat from the friction and the rotation of the single piece causes the metals to combine. A program will then stop the spinning at a specific point, allowing two pieces to be joined at various angles.
3. Orbital Friction Welding :
This type of frictional welding uses motors to spin both pieces at the same time and speed. However, the two pieces are pushed together with their individual axes offset by up to 1/8-inch. The spinning is slowed as the weld is created and the pieces brought into the desired alignment. Pressure is maintained until the weld is set. As with Direct Drive welding, the materials are heated until they reach the temperature necessary to plasticize the metal. For steel, this is about 900 – 1300 degrees centigrade.
4. Linear Frictional Welding :
This type of welding is useful for creating welds along long axes. Instead of spinning, one piece is moved rapidly in a back and forth motion. The two pieces are pressed together as the moving piece gradually heats and forms a linear weld with the other piece. This type of frictional weld is useful for joining parts that have different shapes other than the circular interfaces necessary for the other three types.
Frictional welding is a desirable process in manufacturing because it is considered to be a green practice. Because there is no filler used or external heat source, there are no harmful byproducts produced. Frictional welding allows for multiple different metals to be joined with ease.
The primary drawback to frictional welding is that with the exception of linear frictional welding and friction stir welding, the pieces that are being joined have to be cylindrical. Frictional welding is used in a large number of manufacturing sectors. This type of welding is used in the aerospace, military, and automotive industries, allowing for the production of multiple types of things. They can produce rollers, tubes, gears, hydraulic piston rods, drill bits, connection rods, and pump shafts to name a few products.