How ERP Systems Can Manage Sophisticated Building & Construction Products
by Mashum Mollah Real Estate Published on: 14 April 2017 Last Updated on: 04 May 2019
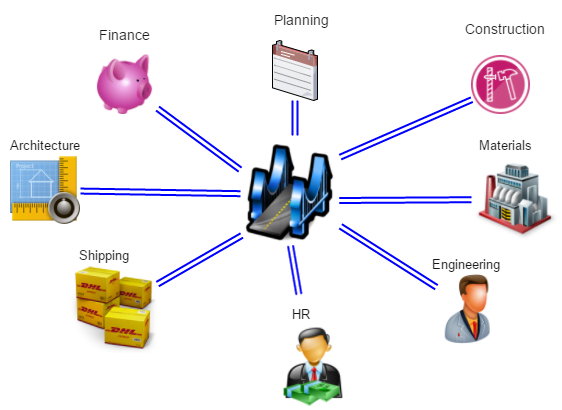
When Donald Trump came to power, among many proposals and plans he mooted a number of major projects. One of the most reported was a $1 Trillion investment in US infrastructure. Such a scheme is massive and presents a wide range of challenges. Politics aside, how do engineers, architects, and contractors go about delivering such projects?
How ERP Systems Can Manage Sophisticated Building & Construction Products:
What is the problem with national infrastructure?
With a country as vast as the USA, there is a massive amount of physical infrastructure, from highways and railroads to bridges and airports. Sadly, many years of under-investment by successive administrations have left much of this essential infrastructure in a poor condition. When depreciation is taken into account, recent investment in infrastructure equates to less than half a percent of the Nation’s GDP. A small amount, if you consider that traffic delays alone cost the US economy more than $50 billion annually.
Each year the Federal Highway Administration release data relating to inspection reports for major highways and bridges. A recent report by the American Society of Civil Engineers has found almost 60,000 or one in nine of major bridges are classed as structurally deficient.
Consider that over 200 million trips are taken over these deficient bridges every single day you can understand how important the issue is becoming. One such bridge was the 1-35W Mississippi River bridge.
Mississippi River bridge collapse:
The Mississippi River bridge was an eight-lane, steel truss arch bridge which carried Interstate 35W across the Saint Anthony Falls of the Mississippi River in Minneapolis, Minnesota. During the evening rush hour on August 1, 2007, it collapsed without warning, killing 13 people and injuring 145.
Similar to all major bridges in America, the bridge was inspected annually and a number of faults had been found including stress cracking in main support beams which classed it as structurally deficient and one of the lowest rated bridges nationwide. A reinforcement program had been planned however this was canceled just months before the collapse.
At 6:05 p.m on Wednesday, August 1, 2007, with rush hour bridge traffic moving slowly across the bridge, the central span of the bridge suddenly gave way, followed by the adjoining spans. The structure and deck collapsed into the river and onto the riverbanks over 80 feet below. Over one hundred vehicles were involved in the collapse.
The following investigation found that there were design flaws in the bridge where major supporting parts were undersized for an increasing load. This flaw was exacerbated by corrosion, which was not found to be a major reason for the failure however it was found that bridge inspectors had not regularly checked that safety features were functional.
The case for change:
It is clear from the number of inadequate pieces of infrastructure and the risks associated with failure that a major investment program is required. As these are to be projects paid for by the taxpayer there is a requirement for frugal management and clear financial accountability as well as on-time delivery of the major projects involved. It will also have far-reaching positive effects for the country. The Economic Policy Institute state that an investment of $18 billion could lead to a staggering $29 billion increase in GDP and the creation of more than 200,000 new jobs.
Implementing major construction projects:
Of course, the plans still have to be completed, let alone be approved by Congress. However, if the green light is given, and it seems that it is a near necessity to ensure that America can keep running. How does such a major series of projects happen?
Anyone who has undertaken even minor home improvements will understand the importance of planning. Ensuring you have the right materials, procuring the correct tools or finding and managing a competent contractor. When you look at major infrastructure projects you need to multiply this by a million (or more!)
Planning for a major construction project is massive, with coordination between contractors, suppliers, engineers and so on.
The diagram above illustrates just some of the major dependencies within a construction project. Managing the timing and cost across such a project involves a massive number of people and organizations. From the multiple US and overseas suppliers to a number of construction and engineering contractors.
The solution is to use a software package which provides a way to collate and manage the otherwise unwieldy amount of inputs and to allow project managers to get an instant view of the state of health of a project on an ongoing basis.
Controlling Major Projects:
Enterprise resource planning systems (ERP) were initially created for the manufacturing industries where they would be used as a suite of computer programs to control inputs and outputs from a process. So for example, the control of the supply of raw materials, tracking of batches through the manufacturing process and the sales and logistics processes.
Enterprise resource planning started to make an impact on the industry in the 1990s, the forthcoming issues with the year 2000 and the millennium bug and introduction of the Euro as a standard currency across Europe acted as a spur for many large organizations to replace their existing computer systems. The major difference from earlier systems was that ERP worked in real-time, allowing a live picture of the state of business across a number of aspects from physical to financial.
The systems allowed for a consistent look and feel across otherwise disparate systems such as HR and procurement and the ability to provide simple ‘dashboard’ views which encompassed these otherwise separate, yet vital areas.
In projects such as the national infrastructure program, a GRP system will be employed. In essence the same but with a focus on Government functions.
The real advantage of such systems is that they offer a true, moment by moment financial view across major construction projects, encompassing inventory, materials and staffing costs.
Historically, construction projects took less of an enterprise view of a project. Each department or trade would have had individual responsibility for estimating, procurement and cost control, leading to islands between which minimal data is shared and therefore a near impossible task to pull together accurate cost control. This has been an issue within the construction industry since its conception. Examples range from the building of the Parthenon in Ancient Greece which shocked Greeks with the final cost right through to New York’s One World Trade Centre which finally cost over $3.8 Billion, more than eight times its original budget.
In a time of collective ‘belt tightening’ and reduction of government projects any steps to stop a $1 Trillion program expanding in cost is vital.
Construction stages – Planning:
The most vital stage of any construction project is the planning, ensuring that an effective plan is created which encompasses all aspects of the project, including visualizing potential issues.
Initial proposals and estimates can be used to generate initial cost estimations and to start the calculation of materials, labor, and trades. These estimates can be rolled into both time and financial models to allow the project to be effectively assessed.
As with any public scheme, there must be transparency. It must be shown that the most cost-effective suppliers have been chosen for the project. On a large scale project, this can involve approaching a large number of suppliers in a request for quote (RFQ) process.
The ERP system can be used to collate the potential suppliers before distributing the RFQ’s. Vendor performance data can be used to support the decision making process before contracts are awarded and managed via a secure ecommerce portal.
The computer system automates much of the process of producing and distributing RFQ’s. Reducing labor costs and ensuring that there is an audit trail of the whole process. Both the requests to vendors and their responses are recorded and stored.
The ERP system will also include material requirements planning functionality to ensure that the materials required for construction are available on time to meet the project schedule. The detailed planning involved allows for optimization of materials to create ‘just in time’ inventory levels reducing storage and production costs. The ERP system can not only calculate when each inventory item will be required it can also be used with the procurement module to automatically generate purchase requisitions to ensure that minimal interaction is required to maintain the pace of building. The system will take on board supplier information such as availability and lead time to ensure that materials are ordered at the most effective time.
Where materials are delivered from overseas there are the additional issues of landed costing and import management. Landed cost is the price of a product once it has arrived at the client site. This cost not only includes the cost of the product itself, but also transport costs, customs charges and duties, taxes, insurance, and currency conversions. The final landed cost can move with changes in fuel prices and currency fluctuations and so it is vital to be able to maintain a regular check and tight control on the actual costs. An ERP system makes this possible. In the past projects may have had to run either with product costs alone or estimates of the landed cost which can lead to budget overruns. The financial infrastructure allows these fluctuating costs to be tracked and reported in real time. The system calculates an estimated cost for the landed cost at the point of creating the initial purchase order, the actual costs can then be entered into the system to update the final material costs.
Additionally, the EPR systems can take away the workload which previously required large shipping departments, managing shipment date, and potential delays and vessel and container tracking.
These functions allow tighter control over incoming materials reducing the risk of over-ordering or not having the correct materials on site when they are required.
Construction Phase:
One of the most complex aspects of any major construction project is to keep it on track, both in terms of schedule and fiscally during the execution phase. Changes to the project specification or unexpected difficulties encountered can drastically alter the project with knock-on effects on scheduling, materials, and contractors. The use of a centralized system allows such changes to be easily and quickly communicated and changes made to ensure that the project is affected as little as possible.
Historically it was difficult, if not impossible to effectively monitor ongoing costs for a live project. The number of variables and different project stakeholders made the task of pulling together data impossible and the day to day payment of suppliers and contractors naturally took priority.
ERP systems allow a way to communicate between stakeholders, with standard interfaces and web-based portals it becomes simple to store data and analyze it in real-time. Allowing for more accurate tracking of overspends or major issues before they escalate.
Post-Construction:
A complex major construction program involves a massive number of individual parts. From small components such as bolts and screws to major architectural elements. If, after construction, it is found that a batch of components was found to be faulty it can be difficult to establish if any of the affected items were used in the project and therefore if remediation work is required.
One of the aspects of a construction ERP system is lot tracing. This allows component elements to be traced by lot or batch numbers. If it is found that there is an issue with a component the affected batch can be traced and identified within the finished construction. This can save considerable time and cost tracing possibly faulty items if there is an issue in the future.
Reasons for using software systems:
The complexity of a major construction project requires a management solution which allows for the many factors to be monitored and controlled. The use of a central ERP provides a way to combine and visualize the data more effectively.
Additionally, the use of efficient systems can reduce project costs. Inventory savings of up to 15% and labor savings of up to 30% are possible as well as a range of time savings and efficiencies when you streamline procurement and supply processes.
Paying for infrastructure:
Much of the major infrastructure projects will be paid for directly by the government, however, there are plans to establish a private/public partnership with funding encouraged from the private sector. However, this seems somewhat unpalatable even to the President’s own party. The major issue is that these projects will require considerable investment at a time when public spending is already under immense pressure.
There is a suggestion that tax credits and usage tax in the form of toll charges could provide the stability of income that the private sector would require. This approach is fine in projects such as toll roads or airports where there is a direct income stream which can be offset against the initial or ongoing investment. However, projects which involve only maintenance on existing infrastructure could prove to be a harder sell to investors.
Late in 2016 Mr. Trump’s economic advisors Wilbur Ross and Peter Navarro detailed how the $1 trillion in infrastructure spending over ten years, equal to $100bn per year or about 0.5% of GDP, could be raised. They mooted that the government would provide a tax credit equal to 82% of the equity investment to reduce the cost of financing. They state that the tax credit plan would be cost neutral as the loss on the tax credit offered to investors would be covered by revenue raised in taxes both on the income from workers employed by the projects and also the taxation on profits earned by contractors.
The devil is in the detail which, at the time of writing, was somewhat sparse. However, it is clear that the nation requires investment. The McKinsey Global Institute states that the U.S. needs to boost infrastructure spending by 0.7% of GDP between now and 2030 purely to meet the demands of the growing economy. It is clear that all parties agree that something must be done, how that will happen is still open to debate.
There is no longer the luxury of time to spend discussing the plans, it is clear that in order to maintain the US position and to keep the country running action must be taken. The risk is, with lead times measured in years or decades for major infrastructure construction projects, by the time the politics are finished it will be too late and the crumbling highways, transport systems, and utilities will be beyond repair!
Read Also: