Cutting Losses From Shipment Damage
by Mony Shah Business Development Published on: 05 October 2023 Last Updated on: 07 November 2023
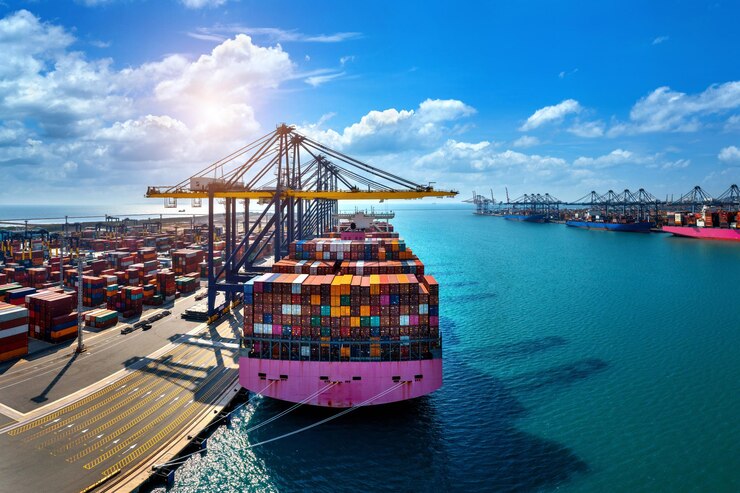
For companies who sell physical products, shipping those products and ensuring that they reach their destination plays a very important role. However, every year companies lose money – and customers – due to damage to their shipments.
This guide provides just a few tips to help ensure this doesn’t happen to your company.
Know the Risks and Adjust Accordingly
Knowledge is power, and that includes knowledge of the potential risks your shipment faces. Some risks are common among all types. These include improper packaging and loading, carelessness and inexperience from the carrier. And issues like container rain and sweat can happen to any shipment. This is where the role of repacking becomes highly significant.
Other risks change due to how the shipment is traveling. For example, cargo travels on planes and ships, which comes with additional risks. Freight travels on the ground. Understanding the unique risks of your shipment gives you the opportunity to address them.
Choose the Best Materials
No matter how your products are traveling, choosing the right packaging materials for the job is crucial. Companies like EPGNA provide materials that can protect your shipment from cargo rain and various other risks. Speaking to such a company can help ensure you have the right protection for your specific needs.
Provide Clear Processes and Proper Training

Before your shipment leaves your warehouse, it needs to be packed, packaged, moved, labeled, and handled properly. If any of these are not completed, or they are completely poorly or improperly, the likelihood of your shipment reaching its location on time, undamaged, or at all is greatly reduced.
The best way to combat this is to have very clear standards and processes for each step. When employees have a simple and clear path to follow, they are more likely to do it. Setting these processes can take some time and commitment, and it might require some trial and error. However, you can lean on the expertise of warehouse management specialists to help.
Once the processes are in place, your employees should have thorough training to ensure that they are clear and capable of managing them. You should also ask for feedback on the processes and consider adjusting processes accordingly. As employees are the front line, they can give you great insight into what works well, what doesn’t, and how things can be adapted.
Additionally, it’s wise to have someone who can supervise and audit processes. This not only ensures that everything is going as planned, but that person can also provide invaluable insight.
Choose an Experienced Carrier
Once the shipment leaves your facility, it’s in the hands of someone else. You want to be sure that the company now responsible for your shipment’s journey is reputable and has experience. Otherwise, you could lose a great deal of money and customers who are relying on your products. Do your research. And don’t be afraid to change carriers if one is not meeting its obligations.
Work With Experts
Everyone needs help and guidance at times, and there is no shame in reaching out for it. Consultants and specialists are available for all aspects of running your business, including shipping and warehouse management. Whether you’re just starting out or have been in business for years, consider reaching out to experts who can help you develop or adapt your processes for the best results.
Read Also: