Manufacturing Of Plastic Bags: How They Are Made?
by Mony Shah Business Development Published on: 04 March 2024 Last Updated on: 05 March 2024
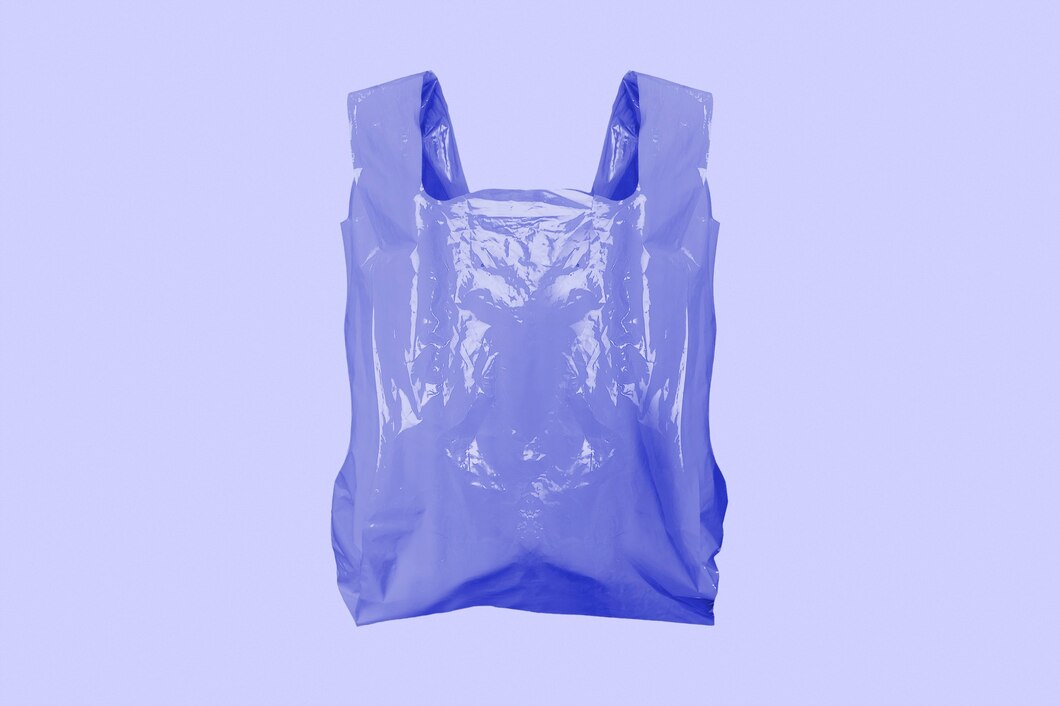
Have you ever stopped to consider how plastic bags are made?
From the grocery store to your home, these lightweight, flexible carriers are a staple in our daily lives. Despite their simplicity, the process of making plastic bags is anything but. It’s a blend of science, technology, and increasingly, a commitment to sustainability.
In this article, we’ll explore how plastic bags are made from raw materials to the finished product you casually toss into your shopping cart. But there’s more to the story.
As awareness grows about the environmental impact of single-use plastics, the industry is shifting towards sustainable alternatives. We’ll dive into both the traditional methods of manufacturing and the innovative practices aimed at reducing plastic bags’ ecological footprint.
Basics of Plastic Bag Manufacturing
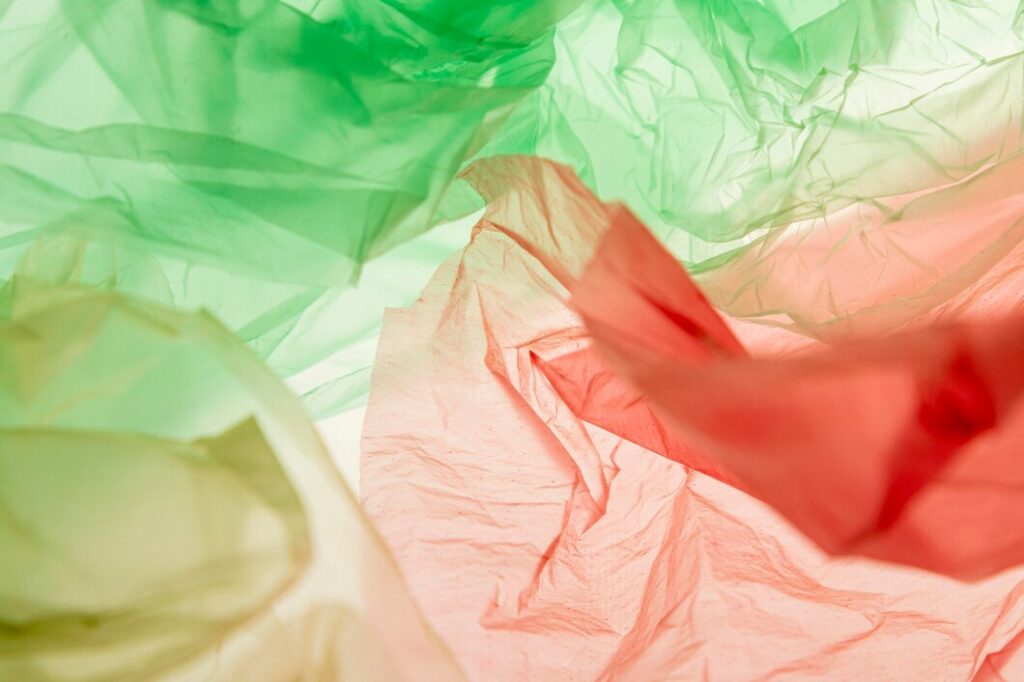
Every plastic bag is made of polyethylene, a versatile and widely used plastic. You might be surprised to learn that this common material originates from resources buried deep beneath the earth’s surface: natural gas and petroleum. These hydrocarbons are not just energy sources but also the building blocks of the plastic bags we use every day.
The process begins with the extraction of natural gas and oil. Through advanced drilling techniques, these essential resources are carefully extracted to minimize environmental impact, ensuring a sustainable supply for manufacturing.
Once extracted, the focus shifts to the refinery, where the oil and natural gas are processed and separated into various components. It’s here that the magic of chemistry comes into play.
The refinement process isolates ethylene, a simple molecule that serves as the monomer building block for polyethylene. Through polymerization, a chemical reaction links these monomers into long chains, creating polyethylene resin pellets. These pellets are the raw material for plastic bags, showcasing the material’s adaptability for various uses, from durable shopping bags to lightweight film wraps.
The process of transforming natural hydrocarbons into polyethylene resin pellets exemplifies the complex and resource-intensive nature of plastic bag production.
This process showcases how technology can transform natural resources into a flexible, strong, and versatile material that we use in our daily live.
From Pellets to Plastic Bags
Turning polyethylene resin pellets into the plastic bags you use every day is quite a difficult process. It involves several stages to convert the raw pellets into poly bags that meet our needs.
Blending Resins and Additives
The first step starts with blending the resin pellets with various additives. This crucial phase tailors the plastic’s properties to suit specific requirements, such as enhanced strength, flexibility, or color.
Additives can include UV protectors, anti-static compounds, or even fragrances, depending on the bag’s intended use. By adjusting the blend, manufacturers can produce bags with a wide range of characteristics, from high-clarity shopping bags to durable, opaque trash bags.
The addition of colorants can also produce bags in any hue, allowing for both practical and branding purposes.
Blown Film Extrusion
Once the pellets are blended with the necessary additives, they move on to the blown film extrusion stage. Here, the blend is heated until it becomes a molten liquid, then extruded through a circular die to form a thin, continuous tube of plastic.
This tube is inflated with air to create a bubble, stretching the plastic to the desired thickness and width. As the bubble cools, it solidifies into a thin film, which is then collapsed and wound onto large rolls. This process is pivotal in determining the bag’s final strength and texture, with the ability to produce films that are either soft and pliable or tough and resistant.
Printing and Customization
The rolls of plastic film then proceed to the printing and customization phase. This stage allows for the addition of branding, instructions, or decorative designs directly onto the plastic. Using techniques ranging from simple one-color designs to complex, multi-color patterns, this customization not only serves marketing purposes but can also provide necessary product information.
Beyond printing, the film can undergo further modifications, such as the addition of perforations for easy tearing or the insertion of handles for convenience. This level of customization ensures that the final product not only meets the functional requirements of carrying goods but also aligns with the branding and operational needs of businesses and consumers alike.
Through these processes, polyethylene resin pellets are transformed into a myriad of plastic bags. Each step, from blending to customization, is meticulously controlled to ensure that the final products meet strict standards of quality and functionality, demonstrating the complex interplay of technology and design in the creation of something as seemingly simple as a plastic bag.
Related Resource: Top 5 Reasons Why Plastic Bags Should Be Banned
Sustainability in Plastic Bag Manufacturing
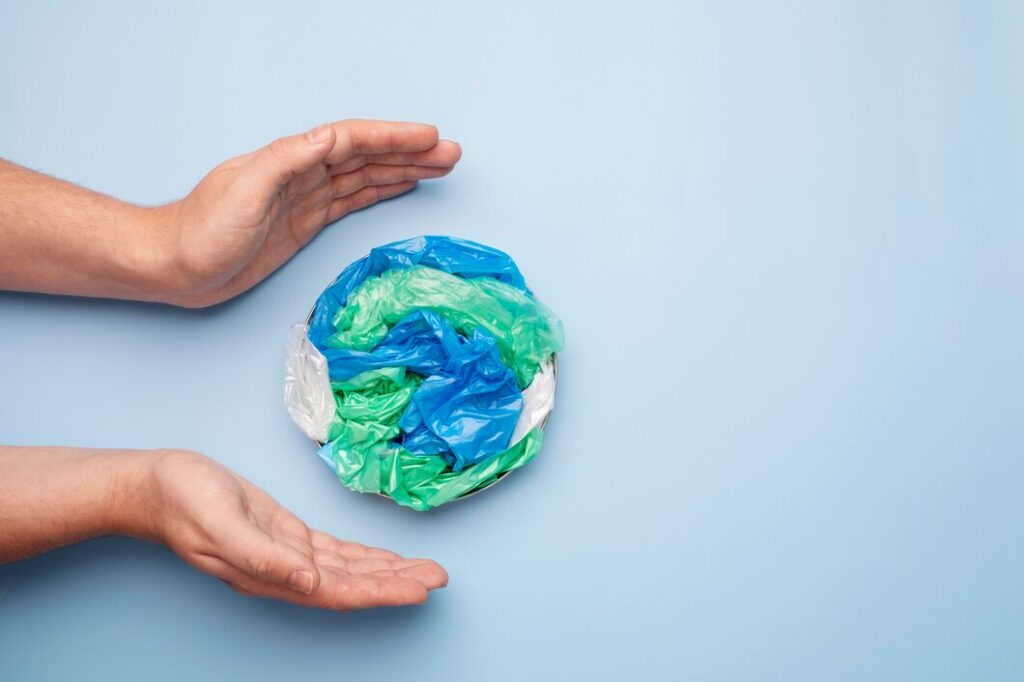
As the conversation around environmental sustainability grows louder, the plastic bag manufacturing industry is listening and responding.
The shift towards more sustainable practices reflects a commitment to reducing the ecological footprint of plastic bags. This transition is not just about compliance with regulations; it’s about pioneering a future where plastic bags coexist with environmental stewardship.
Post-Consumer Recycled (PCR) Resins
A key player in the move towards sustainability is the use of post-consumer recycled (PCR) resins. This innovative approach involves repurposing plastic materials that have already served their initial purpose, and turning them back into resin pellets for new bags.
PCR resins offer a compelling alternative to virgin resins by minimizing the need for new raw materials and reducing the overall environmental impact of production. The benefits extend beyond the conservation of resources; PCR resins also significantly lower the carbon footprint associated with plastic bag production, as recycling plastics consumes less energy compared to producing new polymers from scratch.
Furthermore, by closing the loop on plastic use, PCR resins encourage a circular economy, where plastic bags are seen not as waste but as valuable resources that can be continually reused.
Innovations and Advancements
The industry’s commitment to sustainability is also evident in the development of biodegradable additives and enhanced recycling initiatives.
Biodegradable bags, made possible through the addition of special additives, are designed to break down more quickly under certain conditions, reducing their lifespan in landfills and the environment. This innovation represents a significant step forward in addressing the long-term environmental challenges associated with plastic waste.
Moreover, recycling initiatives have become more sophisticated, focusing not just on collecting and processing plastic bags, but also on creating high-quality, recyclable products from the outset.
Manufacturers are increasingly designing bags with recyclability in mind, ensuring that the end product is easier to process and reintegrate into the manufacturing cycle. These efforts are complemented by educational campaigns aimed at consumers, encouraging proper disposal and recycling to maximize the lifecycle of the bags.
Together, the use of PCR resins, the introduction of biodegradable additives, and the focus on recyclability exemplify the plastic bag industry’s proactive approach to sustainability. By embracing these innovations and advancements, manufacturers are not only mitigating the environmental impact of their products but also leading the way toward a more sustainable future for all.
Final word
The process of creating plastic bags, from raw materials to finished product, is far more complex than most realize. Yet this process that transforms hydrocarbons into convenient carriers also carries an environmental cost. Plastic bag suppliers now have an opportunity to minimize ecological impacts through innovation.
The use of PCR resins, biodegradable additives, and enhanced recycling initiatives demonstrate a commitment to stewardship. But the path forward requires collaboration across the entire supply chain.
As consumers, we also play a role through proper education and behavior change. Simple acts like reusing bags, recycling properly, and reducing overall consumption can drive meaningful progress. By working together, suppliers, retailers, and consumers alike can advance a circular economy where plastic bags are resources, not waste.
Read Also: