5 Composite Parts Designed For Aerospace And Defence
by Arnab Dey Business Development Published on: 21 April 2023 Last Updated on: 19 February 2024
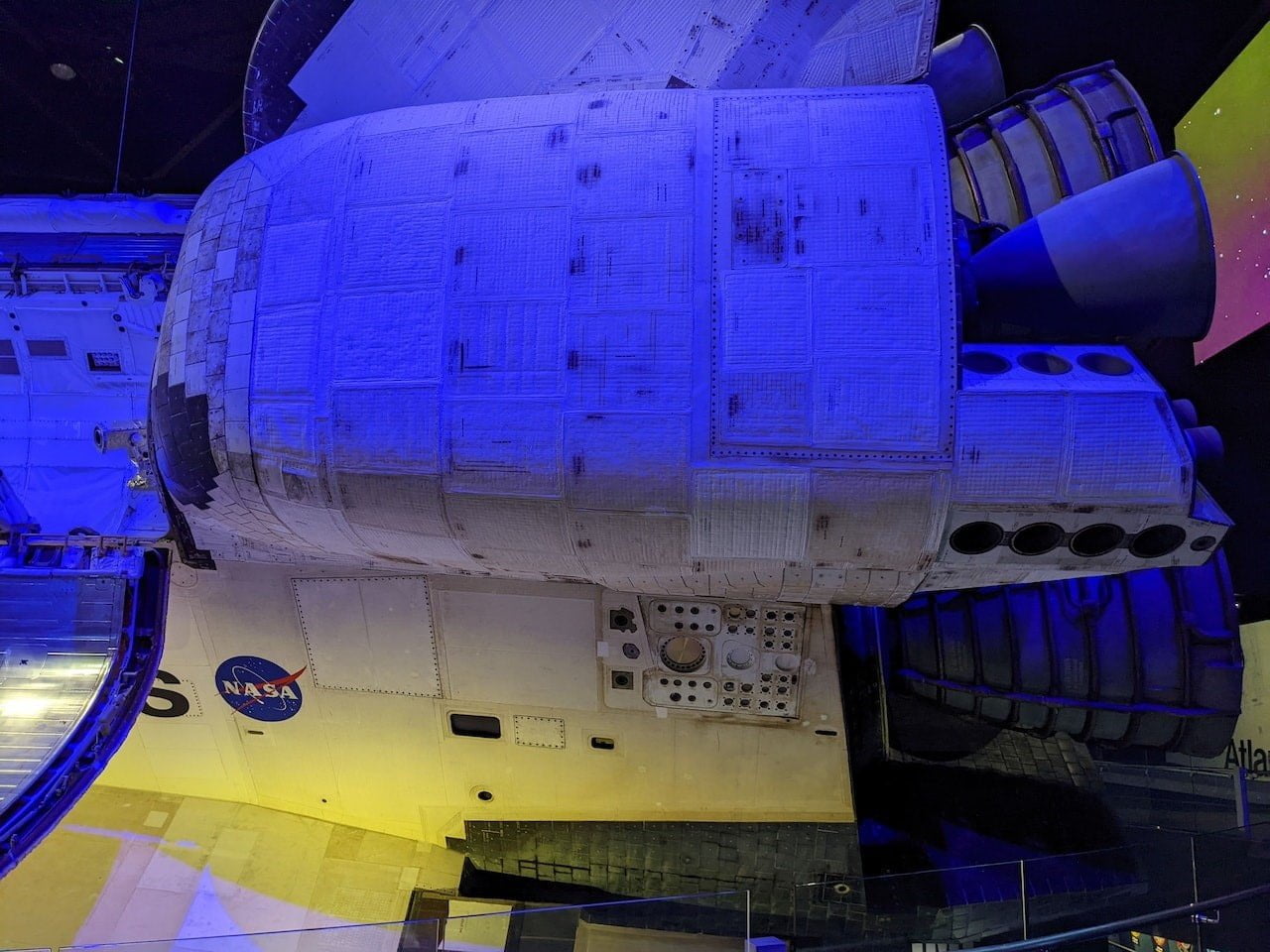
Simply put, countless lives depend on the integrity and efficiency of equipment utilized in both the aerospace and defence sectors, as they both require complex and precise components to ensure safety and reliability. This is why aerospace and defence equipment are increasingly manufactured using composite materials.
Because of the necessity for safe, reliable, and efficient parts in these applications, however, it is absolutely crucial that their components are manufactured by a leading producer of carbon fiber.
Here Are 5 Composite Parts Designed For Aerospace And Defence
Keep reading to learn more about the role of composite parts designed for aerospace and defence applications.
1. Radomes
In the aerospace and defence sectors, radar antennae and other instruments are housed in protective covers known as radomes. Considering the mission-critical functions of these antennae and sensors in communications and detecting and avoiding threats and hazards, protecting them is of the utmost importance.
That’s why they’re commonly manufactured using composite materials that are made to withstand electromagnetic interference and extreme temperature and weather conditions to protect the integrity of these sensitive instruments. Just as important, however, is the ability of composite materials to transmit radio signals.
2. Propeller Blades
Propeller blades are used in aircraft and rotorcraft to create thrust and lift. They are typically made of composite materials due to their high strength-to-weight ratio, allowing them to withstand higher stresses and loads than metal propellers, giving them greater fatigue resistance.
Composite materials also offer better aerodynamic properties compared to traditional metal blades. They can be molded and formed into shapes that are difficult or impossible to achieve with metals, which allows for more complex blade shapes and designs, optimizing the aerodynamics of the blade.
The lighter weight of a composite propeller requires less power to turn, which also improves the efficiency and performance of the aircraft or other equipment.
Finally, composite materials can be designed to have specific stiffness and damping properties to reduce vibrations and noise produced by the propeller blades. This also improves the comfort of passengers and crew aboard airplanes while reducing fatigue and wear on the overall aircraft structure.
3. Engine Components
Composite materials are also used to design and construct engine components such as fan blades, compressor blades, and shrouds used in engines that power vehicles in both aerospace and defence vehicles.
The advantages of design flexibility, high strength-to-weight ratio, fatigue resistance, and acoustic dampening provided by composite materials have obvious benefits in engine parts as well.
However, composite materials are also highly resistant to corrosion and can withstand harsh chemicals and environments. This makes them an ideal choice for engine components that are constantly exposed to saltwater, acids, and other corrosive substances.
4. Wing Structures & Control Surfaces
Wings and control surfaces are some of the most critical components of aircraft and rotorcraft. Wings generate lift and provide stability during flight, while control surfaces, such as flaps, rudders, and ailerons, are responsible for controlling the aircraft’s direction, altitude, and speed. These are typically hydraulically powered and will make use of products such as Skydrol hydraulic fluids to help them operate smoothly and reliably whenever required.
By using a stronger yet lighter material than metal, when wings and control surfaces are made of composite materials, you get a more reliable and fuel-efficient aircraft.
5. Interior Components
Lastly, composite materials are also used in the design and construction of interior components in aerospace and defence vehicles. These components include seats, cabinetry, and flooring. Composite materials are preferred for these components because of their durability, lighter weight, and ease of maintenance.
Read Also: