10 Ways Six Sigma Can Transform Your Small Business
by Ankita Tripathy Business 28 September 2023
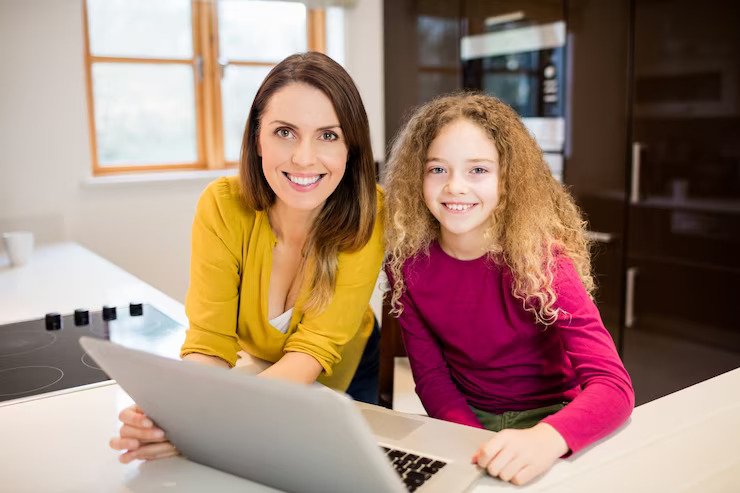
Six Sigma was created by Bill Smith and Mikel Harry in 1986.
It is a method for improving business processes by using a data-driven set of tools to reduce defects and errors. It was originally used in the manufacturing industry but has also been used in many other types of businesses such as healthcare, finance, and service-based companies.
The aim of the Six Sigma method is to achieve near-perfect processes to eliminate defects and errors. The name comes from the idea of achieving a sigma level of six which is 3.4 errors per million processes.
Here are 10 ways Six Sigma can transform your company:
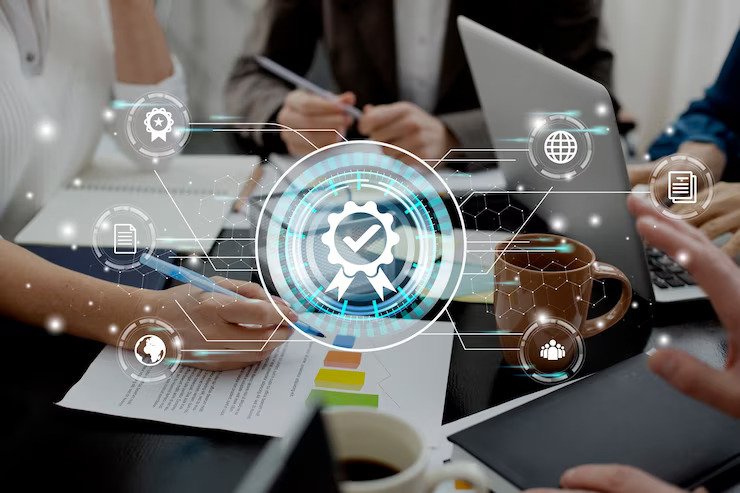
.
.
1. Improving Process Efficiency
Six Sigma can help you identify and eliminate process inefficiencies, reducing waste and saving resources. Today’s tools and methodologies of Six Sigma help managers analyze and improve their business processes, leading to streamlined workflows, reduced cycle times, and fewer errors. By using tools such as process mapping, value stream mapping, and flow charts, inefficiencies can be identified and either eliminated or reduced.
2. Higher Quality Products and Services
The Six Sigma method can lead to higher product and service quality, which can in turn enhance customer satisfaction. By using statistical analysis to find the sources of errors and variations in the manufacturing process, Six Sigma can help create consistent quality, products, and services. Through pinpointing root causes the systematic approach can result in fewer defects in products and services.
3. Reducing Costs
By streamlining business processes, your small business can cut costs related to errors, as well as expenses and time spent reworking failed strategies. Six Sigma can help you identify various forms of waste including overproduction, defects, and excess inventory. The reduction in waste that comes from eliminating unnecessary steps results in cost savings for your company.
4. Applying Data-Driven Decision-Making
Six Sigma relies on data analysis, enabling informed decision-making and better problem-solving. Data is at the heart of Six Sigma and allows companies to make better decisions based on analysis instead of relying on trial and error or intuition.
By using tools such as data charts, histograms, and other data visualization tools, managers and owners can make data-driven decisions. By minimizing guesswork and experimenting, businesses are able to make data-driven decisions that lead to rapid change and eliminate wasted time.
5. Improving Customer Focus
Six Sigma emphasizes understanding customer needs, leading to products and services that align better with market demands. By understanding customer needs and user data, Six Sigma can improve the customer experience. Businesses can gather customer feedback and align their processes and production to better serve their customers and align with their needs.
6. Enhancing Employee Engagement
Six Sigma can bring teams together and give employees a sense of ownership in the progress the business is making. By involving employees in Six Sigma projects, owners and managers can boost morale and generate valuable insights. These engaged employees often provide valuable insight and creative problem-solving to help brainstorm changes and implement solutions.
7. Providing a Competitive Advantage
Six Sigma can provide your business with improved quality and efficiency which will give your business an added edge over competitors who don’t apply these methods. By creating processes that lead to higher-quality services and products, as well as reduced costs, businesses that use the Six Sigma method can be more attractive to customers and more efficient, creating a competitive advantage.
8. Managing Risks
Six Sigma’s data-driven methodology helps identify and mitigate risks and defects, reducing the likelihood of costly issues. By finding these risks and defects and identifying their causes early in the process, businesses are able to anticipate and mitigate risks with less expense and fewer damages.
9. Designing for Improved Scalability
Streamlined processes are easy to replicate, making it easier to scale your business as it grows. Creating streamlined methods, eliminating inefficiencies, and focusing on data through the Six Sigma method allows companies to be in a good position for future growth. By creating efficient, streamlined processes and a method for documenting and analyzing data when the company is small, businesses place themselves in a position to expand without struggling to maintain the high standards of quality and efficiency that they have established.
10. Continuous Improvement in the Future
Six Sigma fosters a culture of continuous improvement, ensuring your business remains adaptable and resilient. By implementing Six Sigma’s DMAIC (Define, Measure, Analyze, Improve, and Control) for current processes and the DMADV (Define, Measure, Analyze, Design, and Verify) for new products and services, your business will continue to get better and better as time goes on. If you regularly assess your processes and enhance them where they are needed, your business will remain adaptable and streamlined even in changing times, new technologies, and adjusting market conditions.
Conclusion
Six Sigma can leverage data-driven analysis, employee engagement, and systematic methods to identify, address, and prevent issues in your business, which should result in improved efficiency, quality, cost-effectiveness, and competitiveness. By incorporating Six Sigma principles, your small business can become more efficient, effective, and competitive in your industry.
Read Also: