4 Tips for Reducing the Transmission of Vibration in Your Machines
by Mashum Mollah Technology 25 April 2019
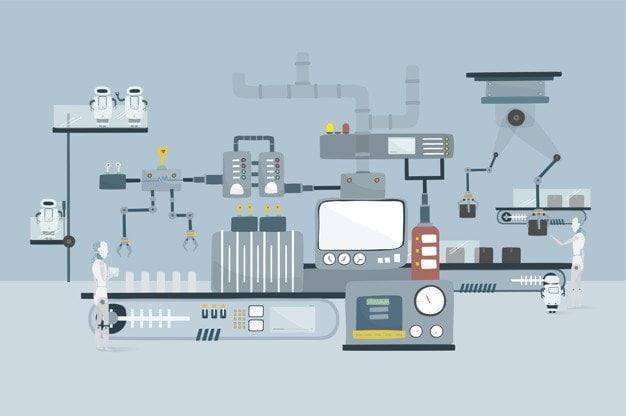
When it comes to industrial machining, vibration can be a serious problem. Your machines could be big enough or powerful enough to shake their own parts loose. Other times the machine is structurally safe, but the vibration can affect other nearby machinery. In some industries that are a serious problem.
Then there are precision machines, which need to be absolutely perfect in their accuracy. A lot of modern day devices have parts which need this type of delicate machining. If it isn’t 100% accurate, it’s useless. Vibrations within the machine can be a problem here though, especially if the machine has aged a little and some parts aren’t quite perfect anymore.
With the massive investment that goes into machinery, it’s important that this doesn’t happen. In 2017 the USA alone spent around $83 billion on machining so it’s clearly a big investment for the market overall – one that nobody wants to see go bad. Thankfully there are ways to help reduce the vibration in your machinery.
1. Make Sure Everything is Properly Connected/Attached:
The first step is to make sure all of the machine parts are properly connected. If anything is loose or slightly out of place, it could be causing extra vibrations. When it comes to machining, parts are usually made to operate in a very specific way. If something is even slightly mis-angled it can bang into other parts and cause vibrations or bad accuracy.
Then there’s also any materials that you’re placing into the machine, or whatever else you’re working on. This also has to be securely placed and, if needed, firmly fastened or attached. That way you get rid of potential inaccuracies and another source of vibration, because again a small gap can cause a lot of movement.
2. Use Rubberized Parts:
Most machines come with high quality parts already, but that doesn’t mean they’re always the best option available. A machine could come with some fittings that allow a little vibration because it doesn’t affect the accuracy or durability of the machine. The problem is that this small vibration can still cause problems for another nearby machine.
It’s sometimes an option to replace certain parts with rubber alternatives, like with grommets. You just need to find a like for like replacement (make sure grommet sizes are the same!) and you can usually swap them out quite easily, or just get a mechanic to do it for you.
3. Ensure Parts Are Not Worn or Damaged:
Parts for all machines will start to wear down eventually. Even if a part is quite new, it can still be vulnerable to sudden damage or a defect. Always maintain your machines properly and they’ll reward you by lasting longer. Worn or damaged parts are a big cause of excess movement in parts and extra vibration.
4. Place Machines on a Rubber Base Layer:
The final tip is a pretty simple one – lay down a base layer of rubber, or a large mat, and place your machine on this surface. You can also use rubber leg caps for some machines. You might need a specific firmness from your rubber depending on the machine and its uses. Having this feature stops most vibration from this machine from even entering the ground, let alone affecting other machines. It doesn’t do much to stop internal vibration within the machine unless it’s being caused by one of our previous points anyway.
Read Also: