Factors Affect CNC Machined Accuracy
by Abdul Aziz Mondal Technology Published on: 28 November 2022 Last Updated on: 04 March 2025
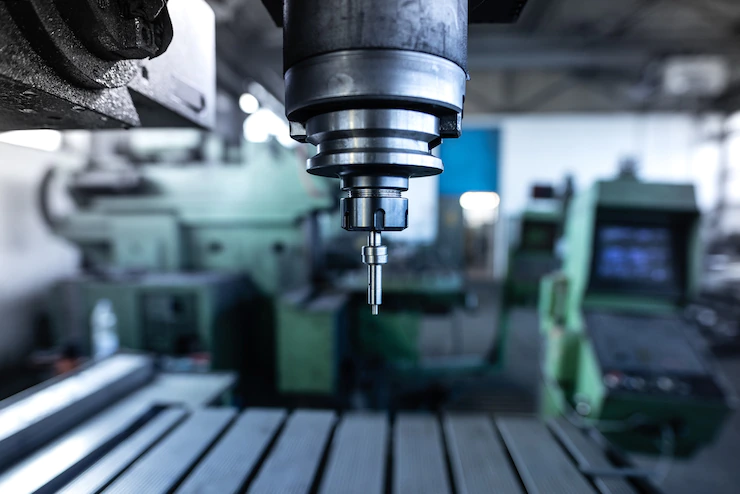
The accuracy of CNC machined parts are affected by numerous factors including the CNC process itself, tooling, materials used, and environmental conditions.
By understanding these factors and taking preventative steps to optimize them, manufacturers can ensure they get consistent, high-quality results when utilizing CNC machining services online or offline.
In this article, we will explore these different factors in detail so you can better understand how they affect the accuracy of CNC machined parts.
Top 4 Factors That Affect CNC Machined Accuracy
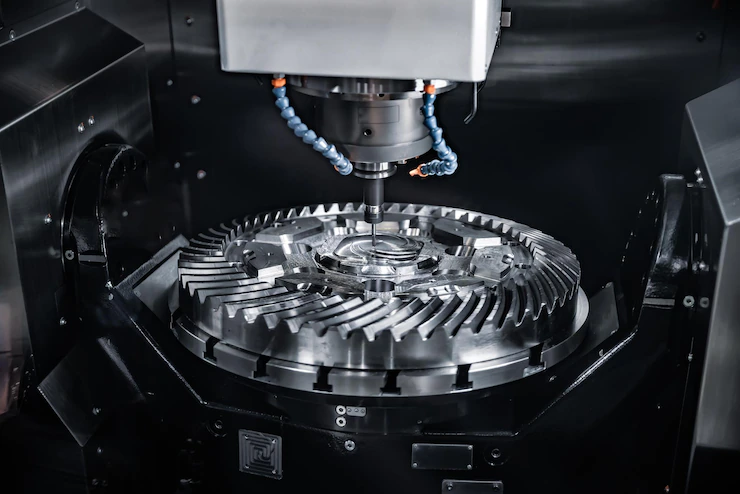
1. Reverse Deviation
One of the major factors affecting CNC machined accuracy is reverse deviation, which occurs when a machine’s cutting tool moves away from its programmed path due to excessive speed or force. This means that the cutting tool will not move as it should and different parts of a machined component could have varying levels of accuracy.
Reverse deviation can cause parts made on a CNC machine to deviate from their intended dimension and tolerance limits, resulting in wear on the cutting tools and significantly decrease productivity due to longer machining times and scrapped items.
To ensure optimal performance, it’s important for operators to routinely check for signs of reverse deviation and address any problems quickly. Regular maintenance such as lubing linear motion guides or replacing worn-out spindles can help prevent reverse deviation from occurring in the first place.
By using precise cutting paths and spindle speeds, operators can also help minimize vibration, which can cause reverse deviation over time.
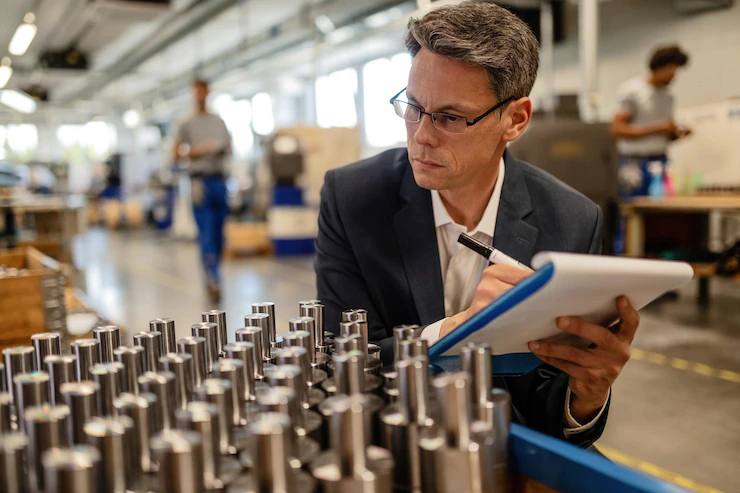
2. Gap Error
A gap error occurs when the cutting tool is not aligned with the surface of the part. This misalignment can cause uneven cutting and lead to gaps between two pieces, resulting in inaccurate dimensions and surface finish on machined parts.
Gap error can also cause burrs, which are raised areas caused by material being forced out of the gap instead of being cut properly. The size and shape of a burr depend on the size and type of cutting tool used as well as how much force was applied during the machining process. If a burr is large enough, it can interfere with other components or affect the performance of a finished product.
In addition to causing dimensional inaccuracies, gap errors can also cause issues with part repeatability. If the same cutting tool is used over and over, it will eventually wear down and create a larger gap between two pieces. This can lead to inconsistencies in machined parts and overall lower quality.
As such, it’s important for CNC operators to pay close attention to their tools and ensure they are properly aligned while machining parts in order to reduce the risk of gap error affecting accuracy.
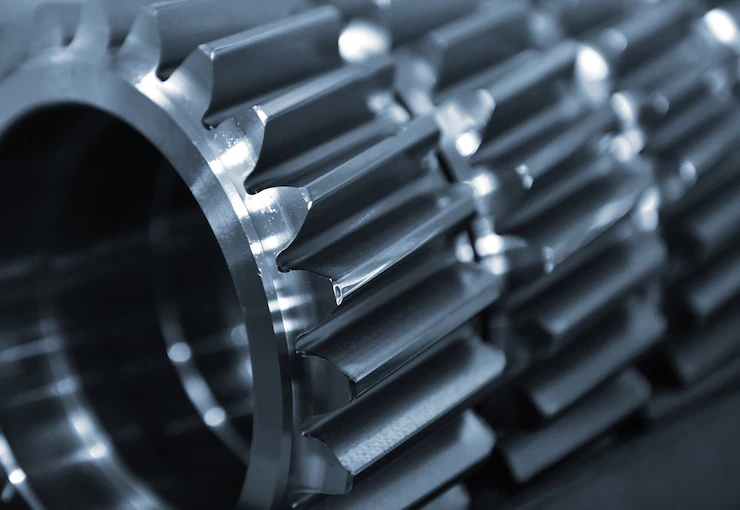
3. Part Position Error
Part position error is caused by several factors, such as angle and distance errors in the positioning of parts, uneven pressure on the parts during clamping or loading, misalignment of tool holders and spindles, and incorrect part measurements. In addition to these factors, environmental conditions can also contribute to part position errors.
When part position errors occur, the accuracy of CNC machined parts will be affected because they may not fit other components properly due to incorrect angles or distances between them.
The shape of the object being machined can also be affected if its dimensions are compromised by part position errors since it won’t produce an accurate final product. As a result, the efficiency of CNC machining processes is greatly reduced when part position errors occur.
To minimize part position errors, manufacturers must ensure that all parts and tools are correctly positioned before starting the machining process.
They should also check for any environmental factors that may influence the accuracy of the process such as vibrations or uneven temperatures in the work environment. With proper positioning and maintenance, manufacturers can reduce part position errors and ensure accurate CNC machined components.
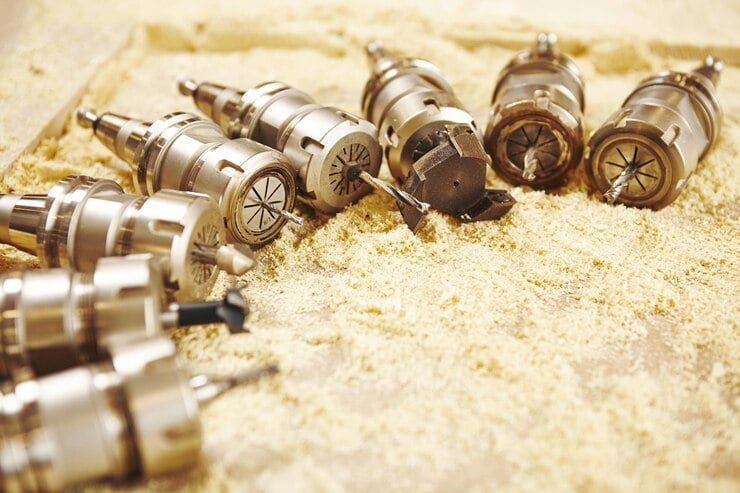
4. Geometric Error Of Machine Tool
This type of error includes misalignment, variations in squareness, taper, variable pitch, runout/geometric form errors, and any other geometrical imperfections. These errors can cause poor surface finish as well as dimensional inaccuracies which will have a direct effect on the quality and performance of the finished parts.
To reduce these errors and ensure maximum accuracy, it is essential to maintain proper alignment within the machine tool. This involves ensuring that all components are properly aligned and that there is no excessive wear or damage to any components such as bearings or spindles. It is also important to regularly calibrate the machine tool and ensure that any necessary adjustments are made in order to maintain the highest levels of accuracy.
By properly maintaining the machine tool, it is possible to reduce geometric errors and improve CNC machined accuracy and precision. This will result in a better quality product and improved performance for the end user. In addition, it will save time and money by reducing waste caused by faulty products and scrapped materials.
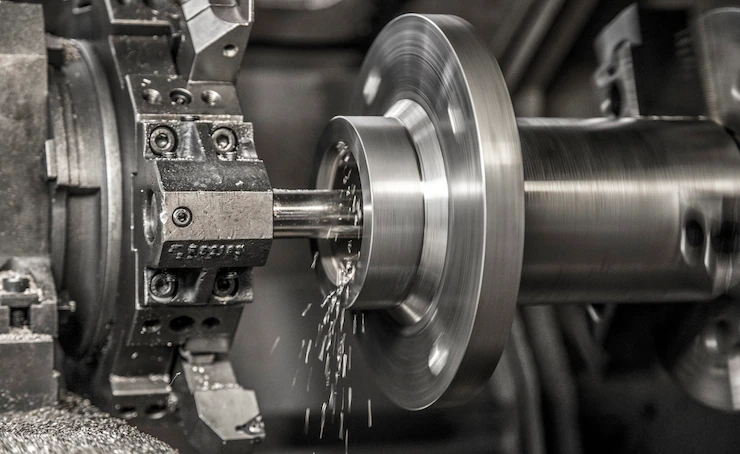
Additional: