How to Minimize Hazards in the Business Workplace
by Abdul Aziz Mondal Business Published on: 06 October 2021 Last Updated on: 30 December 2024
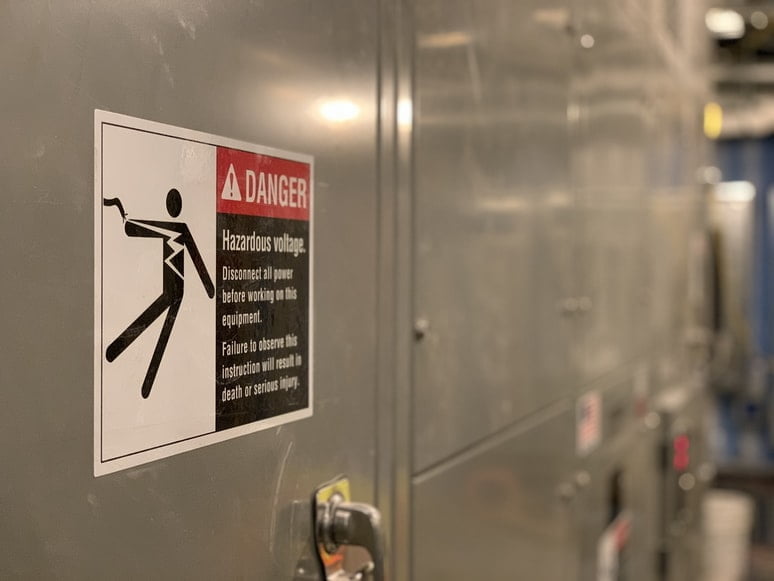
No matter what your workday looks like, you may encounter risks of some kind. Even the office, which is considered a relatively safe space, could be dangerous in some fashion. Workplace hazards are far too common, especially in inherently dangerous industries where safety protocols aren’t followed.
When you take the time to inspect and review your company’s surroundings, you’ll find many hazards hidden to the naked eye. Workplace hazards can always be a possibility, especially if they are blatantly ignored for a long time. For everyone involved, it is important to establish safety protocols across the company. Thankfully, there is a myriad of ways in which your company can minimize hazards to the point of not being harmful.
Here are some ideas on how to minimize hazards in the workplace:
Design & Planning
Many workplaces are the emblems of a particular time period. As time moves on, the physical condition of the workplace may deteriorate, from broken doors to faulty windows. Not only can this look unsightly, but it may end up being a safety hazard to those in the environment.
Renovation, as it turns out, will be your best bet here. Whether you are redesigning a space or starting from scratch, you are granted the opportunity to build safely. Take a look at all the areas that appear to be dangerous or harmful in some manner. It is far easier to directly take action on these areas than leave them unattended for the long term!
WHMIS Labels
In North America, there is a myriad of ways in which work environments are properly regulated. For the most part, every Canadian workplace will implement a WHMIS system of some kind. Known as Workplace Hazardous Materials Information System, it is a considerate form of labeling. Products in and around the work environment could be more dangerous than others.
As a result, it is crucial to designate the proper labeling for these specific products. For example, a cleaning product may be flammable in its composition. If it is labeled with the WHMIS system, it allows the worker to know that care should be taken when interacting with it. WHMIS labeling comes in different forms. Take the time to get familiar with each label through WHMIS training.
Product Replacement
One direct way to reduce a potential hazard is to simply replace it with something safer. As mentioned previously, some products in your immediate environment may be more dangerous than anticipated. First, you do not want to keep this item around forever, as accidents are bound to occur.
In addition, it is far easier to swap out the product with a safer and cleaner alternative. Once you do this, keep it in an area that is out of reach to most workers. It is a team effort to maintain a level of security in and around the workplace. The little things matter, especially when it comes to reducing hazards!
Isolation
If you absolutely must have a potentially dangerous product around, it is important to keep the rule of isolation in mind. This entails making sure that the specific item is put away at a distance to not impact workers nearby. Sometimes, this entails putting up extra security measures to fortify the area.
In strict work areas, you may choose to install some guard rails in and around the specific area in question. Or remote control systems may be chosen in order to operate heavy machinery efficiently. Whatever the case may be, isolation can be an alternative way of prioritizing safety in the workplace.
Ventilation
Most work environments that are considered to be safe will have the right ventilation installed throughout. This becomes much more important during specific seasons, where the weather could have an impact. Or, in the event of a gas or chemical leak of some kind, ventilation will ensure that oxygen isn’t depleted rapidly.
Training
No matter what your role is in the workplace, you should always be familiar with some form of training. Not only can this be a lifesaver in a crisis, but it helps to mitigate the level of risk present as a whole. As an employer, ensure that all of your workers know the ins and outs of workplace safety protocols.
Moreover, you’ll want to ensure that these protocols are reviewed every so often. Accidents or emergencies can happen suddenly, which might exacerbate if the hazard turns out to be worse. Keep your training guidance in a plain and visible view for convenience. Every part of your training matters, and it could be lifesaving in certain scenarios!
Read Also: