Understanding Collaborative Robots and their Functionality
by Abdul Aziz Mondal Technology Published on: 29 June 2021 Last Updated on: 17 September 2024
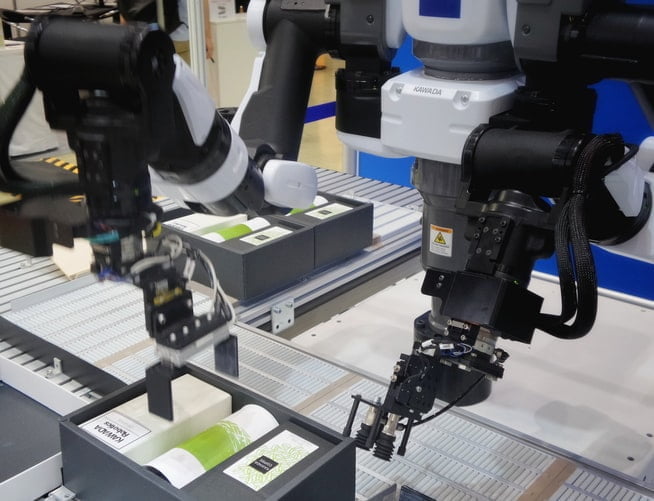
Collaborative robots or Cobots work in collaboration with humans. These industrial collaborative robots are very different compared to other industrial robots that work independently.
This workspace-sharing ability has proven beneficial to both manufacturers and human workers. Cobots come with multiple progressive EOATs, software, and sensors.
All of these factors enable cobots to be at the top of their game. In other words, these EOATs, software, and sensors allow the robot to become more aware of its surroundings.
The current global pandemic saw many businesses make substantial financial losses due to the worldwide supply chain disruption.
Now, businesses are rushing to get back on track, and cobots are helping them do that. These robots speed up order operations and enhance efficiency.
Why Many Industries Use Cobots?
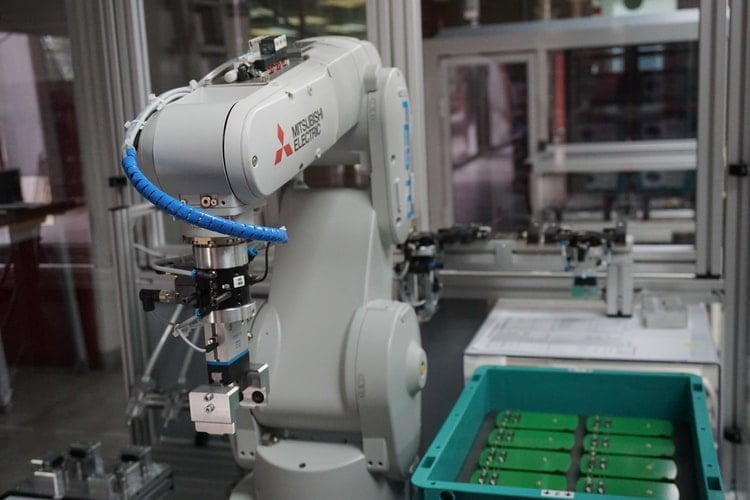
Cobots have a round-like shape, without having a pinch point with internalized motors and wires. When in motion, these robots can also detect force that has been applied abnormally more so, to their joints. They are also programmable such that, they can immediately respond by either reversing or stopping positions when there’s human contact.
Additionally, Cobots can be guided by hand thus making their integration and programming simpler. This means a human can direct the cobot on the desired paths/positions. This frees up human workers for more crucial works. They also come in handy in situations where human workers are injured and are thus unable to perform tasks that require repetitive motion.
Application of Cobots in Manufacturing
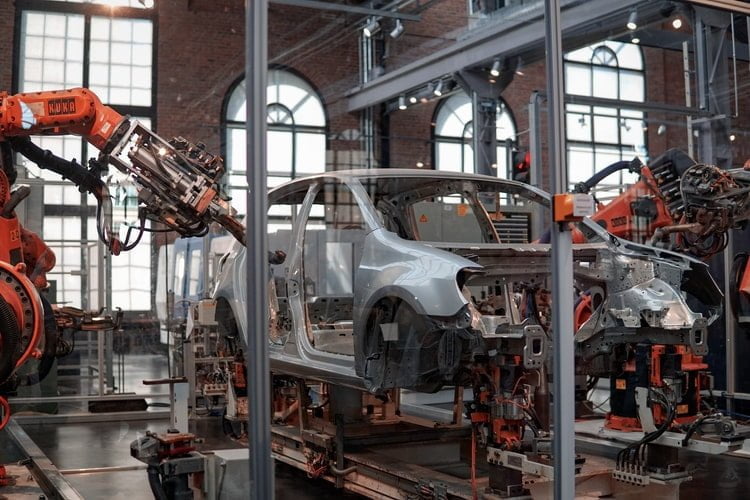
Any business that uses robots in manufacturing and assembly can use cobots. It has been estimated that there are about seventy-four robots for every ten thousand employees globally. Experts also expect this number of robots to increase in the years to come. While collaborative robots do play a crucial manufacturing role, their technology is relatively still young. Cobots are commonly used in packaging and fabrication, testing, molding, CNC machining to quality control assessments.
How Collaborative are They?
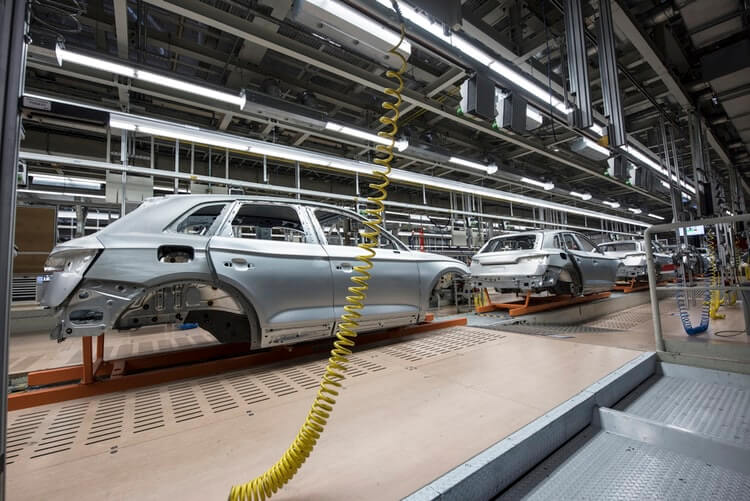
Human workers will start seeing more and more collaborative robots in different workstations. Depending on the workplace, a day with a collaborative robot looks like this: The robot is booted up when the human worker arrives at work then assigns it its tasks and sets it. As the robot works, the human worker takes on other tasks as they intermittently check on the robot in case it will need updating. Once a day is done, and there are no other shifts, the cobot is shut down for the day.
The good thing is cobots are not going to take the place of human workers but instead, work in collaboration with humans.
Comparison of Traditional and Collaborative Robots
The decision for a manufacturer to use either a collaborative or traditional cobot depends on their company’s needs. While there are automation solutions that pose safety hazards at workplaces for associates and operators, cobots are the complete opposite. Collaborative robots have multiple force and sensor motions that make it easy for them to detect people and objects. That way, collisions are avoided thereby creating a safe workspace.
As compared to cobots, traditional robots have been known to need more space and are more dangerous. Even so, they have sheer speed and power. On the other hand, robots are made for specialized, slower work.
Traditional robots can take on large projects and that is why they can be found in almost all industries while cobots are more suited for selected projects. Cobots are also easy to install and less expensive than traditional robots. Their small size means cobots can be used in almost any workstation and do not require the same safety bubble traditional robot needs.
Pros & Cons Of Industrial Collaborative Robots
Industrial collaborative robots come in different shapes and sizes. They are known to ease the load on existing departments and make the job more streamlined.
However, industrial collaborative robots or industrial cobots are hefty investments. Therefore, an investor needs to know the pros and cons of their investments.
Here are some of the most common pros and cons of industrial cobots that every investor should know about.
Let’s go!
Pros
Industrial cobots are very flexible and are generally hassle-free. Industrial cobots are usually smaller and easy to transport and reallocate. This makes them suitable for smaller spaces.
Secondly, the kinesthetic array of these robots makes them super accessible. Therefore, anyone with basic robotics knowledge can use the hand-guiding features of the kinesthetic array.
Subsequently, these robots have quick changeover times. Consequently, you can easily swap out specialized pieces of equipment at will.
The flexible and accessible nature of these robots makes them perfect for small or medium-sized enterprises dealing with multiple products simultaneously.
Another significant advantage of cobots is safety. Industrial robots are known to be dangerous and can end up causing accidents if they are not used effectively.
Meanwhile, cobots are known to be much safer. This is one of the most significant advantages of cobots.
Cons
Cobots are tremendous and can be very flexible. They are known to make manufacturing jobs easier. However, they are best suited for small and medium-sized businesses. This makes them limited.
Cobots are great manufacturing tools for small- and medium-sized businesses. However, industrial collaborative robots struggle when it comes to higher loads.
Cobots generally handle loads of around 5 to 10 kgs. As a result, large-scale industries would need help working with these cobots.
Speed is not the only issue. Cobots are known to be slow. This is primarily due to its light load-bearing capacity.
Therefore, industrial robots might perform less efficiently than cobots. Hence, you might have to sacrifice speed above everything else.
This can be quite a challenge for large-scale industries.
Conclusion
Overall, cobots movement greatly enhances application functionality. Even though they may never replace robots used in the past, they are here to stay. Cobots decrease space robotic units need. The collaborative technology they have offer massive advantages to human workers, production lines, and businesses. When collaborative robots are added to warehouses, the picking process is automated, and human workers are able to maintain great performance without compromising on their safety.
Additional Reading: