Why Is It Important To Reduce Unplanned Downtime In Manufacturing?
by Arnab Dey Business Development Published on: 05 May 2023 Last Updated on: 24 September 2024
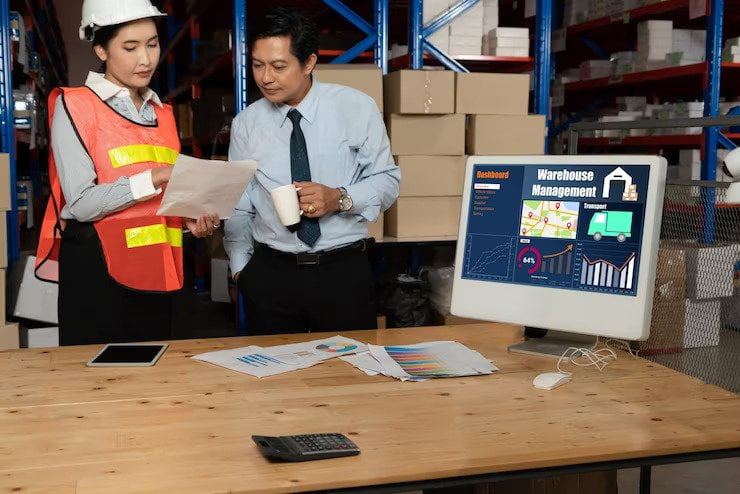
Let’s face it: nobody enjoys having their production line unexpectedly come to a complete stop. But the moment unplanned downtime happens, it can be a real pain in the manufacturing sector, causing delays, messing up schedules, reducing profits, and more.
Do you know as of 2023, the average cost of establishing a manufacturing industry is $33,230? Of course, it is, and this is a huge amount of money for any manufacturer to toy with.
That being said, it is critical in the manufacturing industry to prioritize or place more emphasis on reducing unplanned downtime. By taking proactive steps to identify potential issues and implement preventative measures, you can help keep your manufacturing operations ongoing smoothly and efficiently.
So, what are the steps to take in order to avoid unplanned downtime, and why is it even crucial to reduce unplanned downtime in the manufacturing industry? These and more we will discuss in this article.
What Does Unplanned Downtime in Manufacturing Mean?
When production machinery and equipment suddenly fail, it results in unplanned downtime in manufacturing. Anything from mechanical failures to electrical issues to mistakes made by people could be to blame for this.
Unplanned downtime can be a costly issue for manufacturers, regardless of the cause. It may result in customer dissatisfaction, production delays, decreased output, and lower profits.
Steps to Reduce Unplanned Downtime in Manufacturing
Here are some steps to reduce unplanned downtime in manufacturing:
1. Carry Out Regular Maintenance
Taking the time to carry out regular maintenance can be an important step in helping to reduce unplanned downtime in manufacturing. By scheduling regular maintenance, equipment is kept up-to-date, and any anomalies or potential problems can be noticed and remedied quickly, preventing them from developing into major issues.
Regular maintenance will also ensure that the equipment is working at optimal levels so that productivity goals are met without having to resort to hurried fixes or shortcuts.
2. Implement a Predictive Maintenance Program
With this type of program, you can anticipate problems before they occur and plan accordingly to minimize disruptions in production schedules. This proactive approach to maintenance helps identify potential issues that can be resolved before they lead to an unexpected stoppage.
By monitoring the performance and health of equipment, potential malfunctions can be detected at an early stage, allowing for more efficient repair solutions. Additionally, determining the root cause helps determine suitable preventive measures, which will ultimately result in less expensive repairs and fewer production delays.
3. Train Employees and Invest in Quality Equipment
Investing in well-made, top-brand equipment not only guarantees reliable and efficient functionality but also reduces frequent maintenance requirements and repair calls. Additionally, proper training of employees so that they are able to undertake correct maintenance activities and correctly use the equipment is also necessary for minimizing machine breakdowns.
Not only must employees be taught how to operate each piece of machinery but they need guidance on how to properly carry out visual inspections as well.
4. Implement a Spare Parts Program
A good spare parts program helps make sure your maintenance staff has what they need at their fingertips, so that when equipment malfunctions, repairs happen quickly and efficiently. By proactively stocking the necessary spare part inventory and tracking usage over time, you can ensure your facility stays up and running with minimal loss in production output and cost.
Why is it Important to Reduce Unplanned Downtime in Manufacturing?
After successfully examining what constitutes unplanned downtime in manufacturing and the steps that can be taken to minimize it. Now, why is prioritizing reducing unplanned downtime so crucial? Let’s find out here.
A. Increased Productivity and Efficiency
In the manufacturing line, unplanned downtime can be hugely detrimental to productivity and efficiency. For example, if a machine malfunctions and causes an unexpected stoppage, it can lead to missed deadlines and reduced profits.
By proactively taking steps to reduce unplanned downtime – such as explained above and using machine downtime tracking software that will help you prevent them, you can ensure that machines are operating at optimal levels and that productivity goals are met.
B. Cost Savings
Downtown manufacturing is quite expensive for any manufacturer. For example, replacing a faulty machine part may involve additional costs for labor, equipment, and parts. That’s not all, inventory losses, and energy over-consumption can also contribute to costs.
It is important to try every necessary means to reduce unplanned downtime in order to save your manufacturing industry from these costs.
C. Improved Reputation and Customer Satisfaction
When manufacturing operations are disrupted by unexpected stoppages, it affects the quality of products as well as customer satisfaction. If you have a reputation for producing poor-quality goods or failing to meet deadlines due to machine breakdowns, customers will quickly lose confidence in your abilities to fulfill their orders.
By taking steps to reduce unplanned downtime in manufacturing, you can help ensure that the quality of your products and customer satisfaction remains high, ultimately strengthening your reputation as a reliable manufacturer.
D. Better Safety
Better safety is an essential part of reducing unplanned downtime in manufacturing. Working with dangerous, heavy machinery and complex automated systems can lead to accidents that can cause expensive delays.
Having protocols in place and emphasizing worker safety means fewer incidents, less damage, and higher efficiency of production. Furthermore, safe practices boost morale among workers who know their health and well-being are being taken seriously by their employers.
Besides avoiding injuries and protecting plant equipment, ensuring safety compliance lowers the company’s liability risk. All this adds up to fewer costly interruptions in production due to accidents or compliance failures.
Taking safety into account when planning for production cycles is an important element of staying profitable and productive in the manufacturing industry.
E. Improved Competitiveness
Competition in the manufacturing business is fierce, this is because there are many manufacturing industries that offer the same services you provide. Staying productive and efficient, having a higher quality output, being reliable in meeting deadlines, providing better safety for employees, and increasing customer satisfaction – all these are qualities that will help you stand out in a competitive market.
And on the other way round, your company’s inability to meet up with deadlines, as well as not having a quality output and enablement to stay productive and efficient, will automatically pose a high threat to your business. Therefore, reducing unplanned downtime is crucial to helping your manufacturing operations stay competitive in a rapidly changing landscape.
Final Thoughts
Minimizing unplanned downtime in manufacturing is essential for any business looking to stay competitive and successful.
By proactively taking steps such as regularly conducting maintenance, implementing a predictive maintenance program, investing in quality equipment, and training employees properly, you can help ensure your manufacturing operations are running at optimal levels with minimal disruption.
Ultimately, this will result in increased productivity, cost savings, improved reputation and customer satisfaction, better safety protocols, and improved competitiveness. Taking these steps will help you stay ahead of the competition and remain profitable even in an unpredictable market.
Read Also: