How To Avoid Paper Tearing While Increasing The Splicing Speed?
by Abdul Aziz Mondal How to Guides 27 July 2023
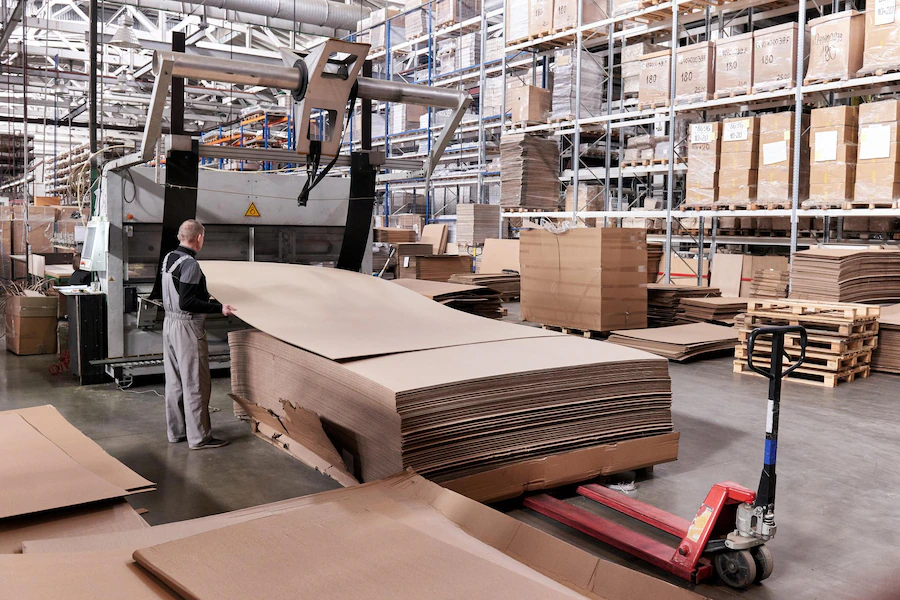
The corrugated board production may be affected by usual downtimes during the splicing phase resulting due to paper tearing or missed splices. As a matter of fact, the web gets pulled in the splicing phase with the help of a splicing tape.
It is mainly found around the draw, whereas the paper roll lying still on the roll stand remains stationary. This is why breakages primarily happen owing to tape not having the correct grip or low-weight papers.
When you make an effort to prevent paper tearing, there is a drastic reduction in the line speed. In this phase, there might be a resultant linear meters reduction that is usually produced each shift and, therefore, to a considerable lost profit.
In addition, when reducing the splicing speed, the production parameters are kept unchanged from those of the set point leading to improper temperature degrees and starch quantity applied to the paper affecting the final product quality.
In addition, for a high cardboard quality, keeping constant web tension is also crucial during the whole converting process. For thinner paper, tension control becomes more and more important.
The corrugator roll stand is normally equipped with pneumatic brakes that emit heat by nature as the friction between pads and discs increases the brake operating temperature. In turn, the heat may cause loss of tension consistency, component wear, and maintenance costs for parts replacement.
Revolution: The Energy Recovery Hybrid Brake
To cope with these problems, Renova has devised Revolution energy-recovery hybrid brake to be installed on corrugator roll stands. Its unique patented design consists of a combination of pneumatic brakes and a regenerative motor, thereby operating with hybrid regulation, always guaranteeing the required braking performances.
Revolution’s brake and motor always work together but combine efforts in variable ways over time; the pneumatic brake, in fact, has only a support function to the motor in daily operations or in the event of an emergency stop. The Revolution’s motor instead takes the lead for everyday activities and conducts the web tension control. Simultaneously, it offers great sensitivity because it has nothing to suffer from heat-related performance.
Revolution is 100% Plug & Play. An easy and fast installation is always ensured, as it is equipped with a customizable flange that allows retrofitting all types of corrugated roll stands.
Read Also: Improving Productivity With A Pallet Changer Machine
Splicing Without Paper Tearing
When splicing, the Revolution’s motor makes the axis roll accelerated right when the splice is getting directed. Hence, getting rid of its initial inertia is the main concern here, rather than paper web pulling.
By accelerating the roll during the start-up phase, the splicing phase can proceed without slowdowns, preventing waste and reducing missed splices, and bringing the new roll up to line speed more quickly and without causing web tear out.
Revolution, in fact, allows every corrugator the opportunity to increase productivity by splicing with at least 25% faster line speeds, to work with lower-weight papers, and to increase the quality of the final product by working with more proper temperature and starch parameters.
Regenerative Braking
The Revolution hybrid brake is the most eco-friendly and sustainable choice available on the market.
As mentioned before, each corrugator makes use of a pneumatic brake emitting thermal energy that generally goes off in the surrounding. The Revolution system might help in partially recovering the undisturbed energy. To say simply, the motor gets transformed into the brake’s thermal energy.
It is otherwise ridden as heat inside an electrical energy roll stand weighing up to 2kWh. This is later again utilized in the plant’s electrical line right away through the original plug provided with Revolution.
This is possible thanks to the Revolution’s certified system that corrects the power factor and allows the plant to instantly benefit from the energy saved.
Furthermore, due to its support function, the Revolution’s brake works less, and brake pad wear is further reduced,
with positive consequences on maintenance requirements and costs for parts replacement. And less pad wear means less powder pollution and a cleaner working environment. Revolution’s motor instead does not require any maintenance as no components are subjected to wear.
Industry 4.0
The 4.0 Industrial Technology or the Big Revolution: In the integrated system, one might find an easy-to-use and intuitive control panel that helps in devising a direct dialog. The latter is established within the production system around ERP. moreover, the cabinet consists of each electronic component, thereby joining the dots with Revolution’s plant electric line.
Increased Safety Level
The motorized rewind of the reel is possible through the control panel. This eliminates any injuries by eliminating manual intervention and ensures a higher safety level for the operator.
So, what is the delay?
An ever-changing Revolution is waiting for you!
Read Also: