Why Buy A Used Machine Tool?
by Abdul Aziz Mondal Business 18 January 2024
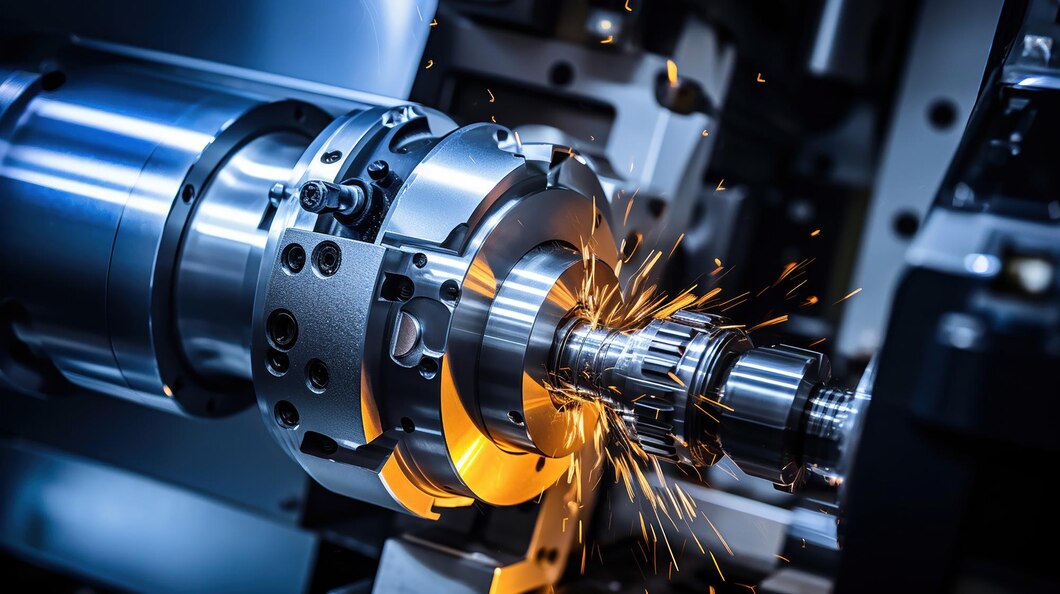
Deciding whether to go for new or used machine tools can be tricky.
Running a successful manufacturing or fabrication facility requires making smart choices about equipment, buying top-notch raw materials, and managing your workforce.
While some managers might think about saving money by purchasing used machine tools, it’s important to note that new equipment, despite being an initial investment, often proves to be a wise long-term decision, paying off quickly.
And to be honest, it’s quite easy to find used CNC lathes for sale. So, the availability of a used product tends to be much better than a new product as well.
Benefits of Using a Used Machine Tool
While getting new assets for your business is often the top choice, buying used equipment has its perks too. Here are a few things to think about —
1: Decreased Expenses
Purchasing secondhand industrial machine tools comes with a significant cost advantage. These used machines are generally more budget-friendly than brand-new ones, allowing companies to boost their manufacturing capabilities without straining their finances.
This is particularly advantageous for top-tier machines that can be extremely expensive when bought new, often costing hundreds of thousands of dollars.
Furthermore, as used equipment has already experienced depreciation, its resale value tends to decline more gradually compared to new machinery over time.
2: Machine in stock and available
Opting for used industrial machine tools comes with the perk of quicker availability compared to brand-new equipment.
Choosing used industrial machine tools means you can get them quickly, unlike new ones that need to be ordered and make you wait.
Used equipment is often ready for immediate purchase or can be obtained within a few days. This is great for businesses with urgent projects, as there’s no long wait for new equipment.
3: Offers Reliable Performance
Contrary to what many think, used industrial machine tools aren’t always unreliable. Some of these machines have been well cared for and can work reliably for a long time. Plus, many used machines come with warranties or service plans, giving buyers extra confidence.
4: Comes with a Variety of Options
Choosing second-hand industrial machine tools provides more options compared to buying new machines. Businesses can discover machines that are no longer in production or models that have been upgraded with new features. This variety enables companies to find machines tailored to their specific requirements, avoiding a one-size-fits-all approach.
5: You Know Exactly What You Are Getting
Choosing new equipment eliminates the risk of unexpected issues. Unlike used machines that might have hidden internal problems, new ones come straight from the factory in top-notch condition. This means you don’t have to worry about preexisting problems, ensuring a smooth and trouble-free operation.
6: Environment-Friendly
Choosing used industrial machine tools is a green choice. After all, if you use the same tool or machinery again, it will be easier for you to cut down the carbon emissions related to a brand-new machine as well. Such an eco-friendly option fits pretty well with the ever-so-increasing focus on global sustainability in the current business world.
7: Can Hold Its Value
If you maintain your used machinery well, it holds its value.
As a trusted auctioneer, we’re picky about the quality of assets we buy, preferring equipment with a maintenance history. If you’re looking to sell, contact us for a free valuation, and we can discuss the right sales process.
Once you have your used assets, keep detailed service records.
It’s not just for tax purposes but also crucial when you decide to sell later on. Prospective buyers will want to know about the machinery’s service history, and the more details you provide, the better chance we have of finding a buyer quickly at or close to your asking price.
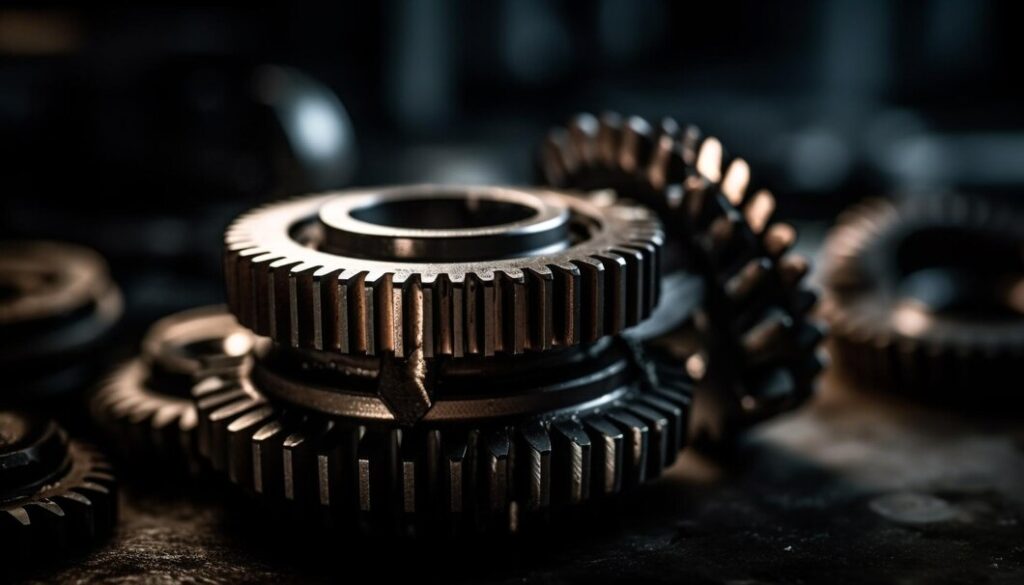
How Can Machine Retrofitting be Helpful?
Machine retrofitting and engineering involve evaluating and upgrading existing machines instead of buying new ones. It’s like giving an older machine a boost by adding more energy-efficient features or automation.
Retrofitting lets you continue using your older machinery until a newer model is available.
This practice isn’t new; the automotive industry has been upgrading older vehicles with modern technology for years, improving performance, efficiency, and safety.
While machine engineering might seem conservative, retrofits are becoming more common across various engineering fields, from energy conversion to renewable energy.
Some examples of machine retrofitting can include —
- When a business needs more productivity, corrosion protection, or added features, it might replace an old machine.
- Upgrading involves adding electrical sensors and accessories to boost the machine’s capabilities.
The Benefits of Machine Retrofitting
A: Decreased Downtime
Newer CNCs last longer between breakdowns compared to older ones.
The companies making the hardware have used better technologies for more reliability. The screens for operators and maintenance are advanced, showing problems in pictures and how to fix them quickly. Also, more technicians know how to help with the new CNCs, making it faster to find and fix issues compared to older controllers.
B: Can Improve Safety
Upgrading to modern Safety Rated CNCs improves the safety of machine centers.
These CNCs let you include I/O in the safety programming, reducing the need for extra hardware like safety relays. Unlike older relays, modern ones provide clear troubleshooting guides, making it easier to find and fix issues. When updating controls, it’s a good idea to do a Safety Risk Assessment to make sure the right safety level is reached and risks are minimized.
C: Reduce Your Overall Costs
Choosing between a CNC retrofit and getting a new machine is about making the most of the value in older machine frames, known as ‘Good Iron.’ These frames are sturdy and costly to replace. By retrofitting, you keep existing foundations, tooling, and fixtures, saving money.
Retrofitting a CNC might also give a quicker return on investment (ROI) compared to buying a new machine. The project cost is usually much lower than buying new. Some customers depreciate assets over the long term and can’t write them off immediately.
A CNC retrofit brings new life to the machine with updated controls, extending its service life. Some retrofits have had a return on investment in as little as six months, while larger ones typically take less than two years.
Read Also: