Maximizing Efficiency: Top Strategies for Manufacturing Process Optimization in 2025
by Pijus Maity Our Blogs 21 February 2025
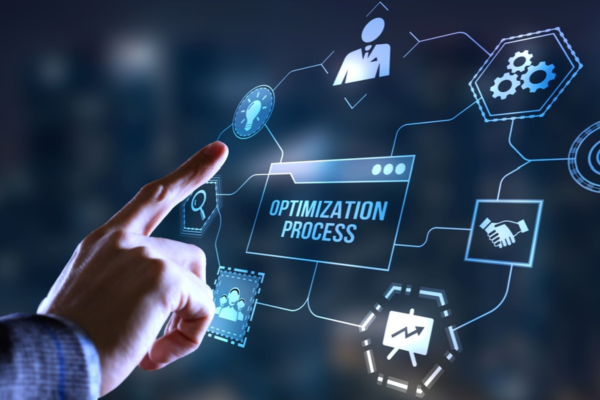
The manufacturing industry is getting more unpredictable in 2025. From supply chain hiccups to global uncertainties like inflation, manufacturing process optimization is becoming a must-go approach while facing real problems that are not temporary but the new normal.
In such situations, waiting for stability is only a wish that will lag you behind. Instead, it is time to seek operational agility, make data-driven decisions, and ensure smart planning for uncertainties.
Imagine this: You have an opportunity to boost productivity by 30% just by considering some critical changes in your normal manufacturing process. Sounds incredible, right?
Well, with smart manufacturing solutions, you can improve your business efficiency. Whether you suffer from high operational costs or supply chain disruption, investing in the right place and addressing the changes you need to build a strong manufacturing ecosystem will ensure manufacturing success.
Before that, understanding the key challenges for manufacturers in 2025 is essential.
Therefore, settle in and read until you find a comfortable solution!
Main Challenges Manufacturers Facing in 2025
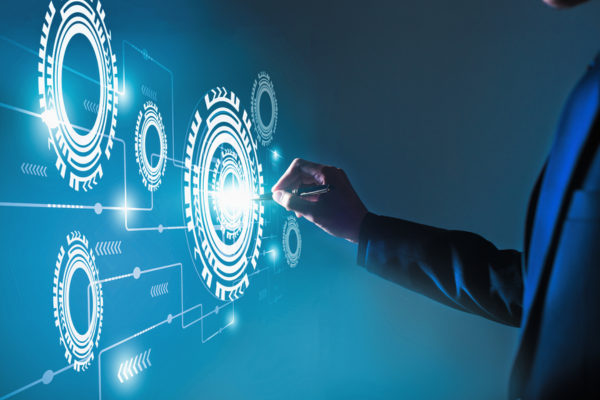
From the boardroom to the factory floor, manufacturers face a tough climate when handling the quality and quantity of projects. Inflation has been the foremost internal obstacle manufacturers have faced for the last two years.
Apart from that, some other obstacles pushing strategic efforts behind are-
- Rising energy cost
- Cybersecurity issues with IT and OT networks
- Shortage of skilled workforce (lack of relationship between technology and people)
- Supply chain instability
Among all these factors, workforce issues are both internal and external obstacles for the manufacturing industry. Onboarding new employees is no longer an issue in 2024. However, attracting employees with desired skill sets is becoming hard to maintain.
However, automation, integration, and on-time monitoring led to business manufacturing process optimization while reducing skill gaps and encouraging data management. Some of the efficient smart manufacturing technologies are-
- MES (Manufacturing Execution System) integration
- DCS (Distributed Control Systems)
- APM (Asset Performance Management)
- SCP (Supply Chain Planning)
- ERP (Enterprise Resource Planning)
- QMS (Quality Management Systems)
Manufacturers are stepping up to utilize these resources. As a result, in 2024, we have seen a 30% surge in technology investment.
Smart Manufacturing Solutions to Optimize Manufacturing Processes
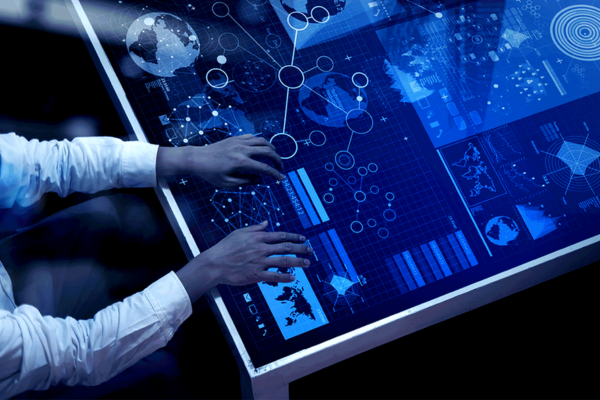
In 2025, the call for manufacturing process optimization is louder than ever. The need for agility amid rising costs, supply chain uncertainties, and skilled labor shortages seeks optimal solutions in manufacturing.
1. Implementing Lean Manufacturing Principles
Lean manufacturing principles focus on minimizing waste while maximizing productivity. While reducing operational costs in manufacturing is one of the most critical concerns with the rising energy costs, lean manufacturing offers an improved process.
By adopting these principles, manufacturers can streamline operations and reduce waste. Therefore, they ultimately enhance their product quality while ensuring minimal waste.
Implementing invaluable techniques like value stream mapping finds out areas of waste in operations, leading to better waste management and continuous improvement. Employees who are involved in lean manufacturing are accustomed to risk areas to reduce waste while ensuring ‘Kaizen.’
A real-world masterstroke: Toyota once went with the Toyota Production System (TPS), which helped them eliminate waste while maintaining high quality.
2. Adopting Industry 4.0 Technologies
Industry 4.0 reflects the industrial revolution that fosters interconnectivity, machine learning, automation, and real-time data. Some factories are smart enough to run it on their own. However, other manufacturers outsource the processes to adapt to more profits.
However, this transformative approach in manufacturing process optimization accumulated with advanced technologies like-
- Internet of Things (IoT)
- Artificial intelligence (AI)
- Automation
A real-world masterstroke: Bosch, by utilizing Industry 4.0, used IoT in their production line to ensure a 10% production increase and a 25% reduction in machine downtime.
3. Utilizing Advanced Data Analytics
Data is a powerful tool for enhancing decision-making and strategic planning. It is all about improving your existing processes with better insights. This way, manufacturers try to identify trends and predict future demands.
Moreover, advanced analysis helps us make quick decisions in changing market conditions. The more data you have, the better you can utilize it to schedule and improve inventory management. Software like PowerBI and Tableau encourage better data management while minimizing human errors.
4. Optimizing Supply Chain Management
Advanced supply chain management deals with costs and time in the manufacturing process. In 2025, manufacturers must adopt a holistic view of their supply chains, leveraging technology to enhance visibility and collaboration.
You can implement tools like Manufacturing Execution Systems (MES) to monitor real-time supply chain performance. Also, it delivers better demand forecasting and inventory management solutions.
A well-optimized supply chain enhances responsiveness to market fluctuations. Therefore, it reduces external disruptions.
5. Investing in Employee Training and Development
Even with advanced technologies in place, skilled personnel are essential to drive optimal manufacturing processes. Investing in employee training and development ensures workers possess the necessary skills to operate sophisticated machinery and interpret data effectively.
Organizations should foster a culture of lifelong learning, offering continuous professional development opportunities and upskilling programs. The more you try to instill knowledge among your employees, the better they will address issues and make continuous improvement a habit in no time.
Go for Sustainable Manufacturing with Technology
Focus on sustainable manufacturing that reduces the environmental impact on your manufacturing process and reduces the cost of operations. Sustainable manufacturing process optimization leads to eco-friendly practices to enhance your brand reputation.
For instance, Patagonia’s environmental efforts, like using organic cotton and recycling polyesters, helped it reduce waste while thriving in the fashion industry.
Therefore, you can focus on a lean manufacturing process and utilize energy-efficient equipment to generate more revenue. This also ensures industrial standards in the international market for a seamless manufacturing experience.