Protecting Concrete Infrastructure With Biogas Membranes
by Abdul Aziz Mondal How to Guides Published on: 27 December 2023 Last Updated on: 07 March 2024
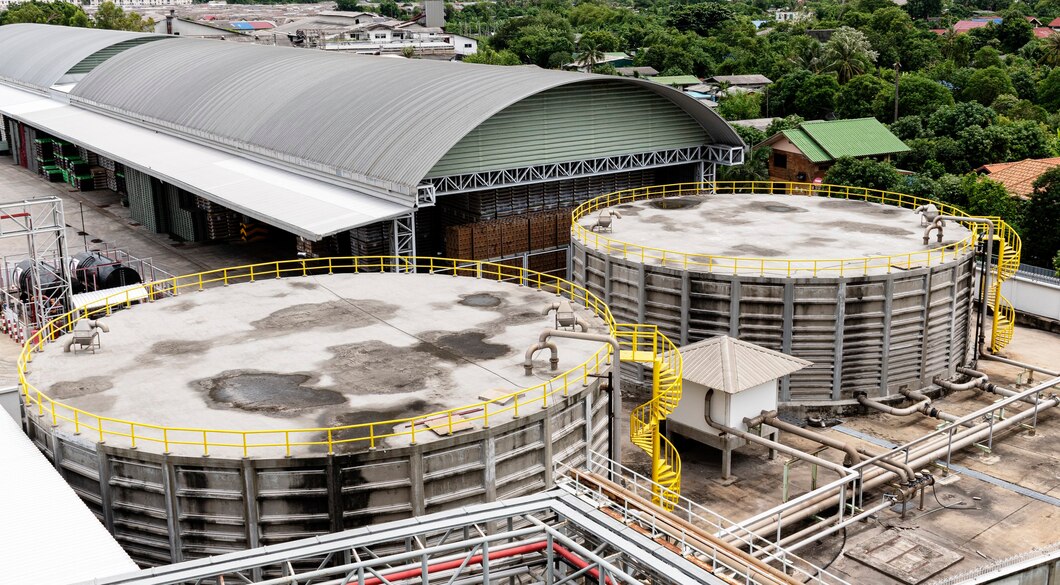
For concrete structures exposed to corrosive biogas environments, impermeable barrier membranes provide critical protection. Read on for an overview of biogas conditions and specialized membrane options as per biogasmembrane.com for preserving concrete integrity.
Understanding Biogas Corrosion Risks
Biogas produced by decomposition in landfills and wastewater systems contain aggressive compounds like hydrogen sulfide. These acidic substances penetrate and severely degrade concrete over time.
Evaluating Damage Modes
Depending on exposure levels, hydrogen sulfide corrosion erodes cementitious matrices through chemical interactions and microscopic cracking. Biogenic sulfuric acid dissolves concrete surface layers.
Assessing Environmental Conditions
Consider temperature, relative humidity, H2S concentrations, and exposure time when selecting protective membranes. More extreme conditions require enhanced barriers.
Common Membrane Materials
Thermoplastic polyolefin membranes offer cost-effective protection. Polyvinyl chloride and polypropylene materials balance performance with affordability. Polyethylene provides chemical resistance.
Specialized High-Performance Membranes
Where extreme acidity or pressure exists, reinforced composite membranes made of butyl rubber, polyurethane, or epoxy offer advanced protection for critical assets.
Installation Best Practices
Proper surface prep, overlaps, seam reinforcement, and puncture avoidance during backfill ensure the membrane forms a continuous protective barrier-free of perforations or leaks.
Inspection And Maintenance Planning
Schedule routine visual monitoring of membrane integrity and early repair of mechanical breaches, along with testing for breakthroughs. This prolongs functional lifespan.
Added Benefits Beyond Corrosion Resistance
Membranes also protect concrete protection from soil chemicals, water infiltration, and root penetration. Radon barrier membrances value-add for buildings.
Partner With Experienced Applicators
Work with reputable contractors experienced in protecting concrete water infrastructure like pipes, tanks, vaults, and digesters from biogas exposure to ensure quality.
Balancing Protection With Economics
While the most robust epoxy-based membranes provide extraordinary chemical resistance, polyolefin materials may sufficiently protect facilities with moderate H2S levels at lower cost.
Defending concrete against biogenic degradation is essential for extending the service life of wastewater infrastructure. Specifying and installing high-performing membranes tailored to unique environmental conditions provides asset owners with cost-effective insurance against corrosion damage over decades of service.
Top Industries Requiring Biogas Membrane Protection
Due to high hydrogen sulfide exposure, the following sectors commonly rely on protective membrane barriers for concrete structures:
Municipal Wastewater
Protecting containment tanks, pipes and digesters from acidic attack preserves water treatment assets.
Landfill Management
Lining landfill subsurface walls and leachate containment systems safeguards environmental integrity.
Mining Operations
Membranes shield mine infrastructure like heap leach pads from chemical assault.
Agricultural Projects
Digester tanks, manure lagoons and silage storage benefit from barrier coverage.
Industrial Wastewater
Refineries, chemical plants and other facilities contain aggressive effluents with membranes.
Food Production
Membranes protect concrete substrates across beverage makers, meat processors and more.
With expertise tailored to each unique project, reputable membrane applicators enable cost-effective, long-term concrete protection across corrosive environments.
Read Also: