Variable Speed Drives: The digital Servo Drives
by Mashum Mollah Technology 25 July 2019
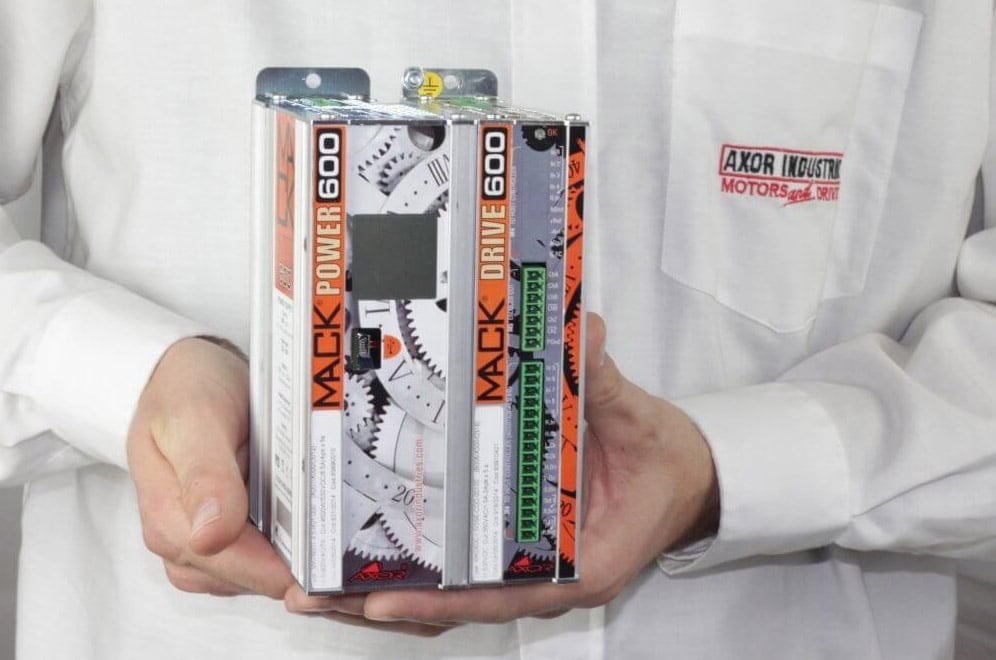
The variable speed drive sector is one of the most important in industrial automation and includes both products as well as systems.
The need to drive machines and processes at variable speeds is present since the beginning of the history of the manufacturing industry. The reasons can be summarized as:
- Need to have different speeds for different states of production;
- Adjustment of the quantities produced in the unit of time (machine cycles);
- Management and control of the start and stop phases;
- Maintaining a constant speed as the load and other parameters that have influence change;
- Adjustment of other critical quantities (torque, pull, position);
- Energy savings.
The industries and processes where this product is mostly used are:
- Metallurgy (casting, hot and cold rolling mills, treatment and finishing lines);
- Paper and graphics (winding machines, coating machines, calendars, printing presses or packaging);
- Rubber and plastic (mixers, extruders);
- Textiles and fibers (spoolers, ironing lines);
- Lifting and transport (cranes, elevators, conveyor belts);
- Machine tools (for spindle and axis control);
- Chemistry and HVAC (pumps and fans).
Fundamental for the stability of the system is the closure of the speed and position axis ring. The transducers used for this purpose provide an analog or digital signal.
From the constructive point of view there are various types of transducers:
- Capacitive / inductive, related to the use of proximity sensors,
- Optical, based on the use of photodiodes,
- Magnetic, based on hall effect.
From the operational point of view, two main types can be considered:
- Analog (tacho, resolver),
- Digital (incremental or absolute encoders, optical lines, digital servo drives).
The Resolver is an absolute transducer in the turn angle used both as a motor speed detector and as a position transducer. It is a rotary transformer composed of a primary and two secondary phase-shifted by 90 °. It is a less precise component of the encoder, but definitely cheaper.
The incremental encoders supply a continuous cycle pulse train and are therefore not able to give a unique position value of the axis. There are incremental encoders that work with sinusoidal signals, others with square-wave signals.
The use of digital servo drives with 32-bit processor allows obtaining very high internal resolutions of the order of millions of pulses/revolution with very high precision.
The continuous increase in the performance required of the transducers, the need to simplify the wiring as much as possible, and the related installation costs, has led to solutions based on coded interfaces. They are digital, synchronous, bidirectional, and coded interfaces, capable of transmitting both incremental and absolute position values and carrying out the necessary data storage.
The drives of the first generation, prior to the advent of microprocessor systems, are analog and have been realized with the use of discrete components and logics. The advent of digital technology in the 1980s allowed, thanks to the introduction of microprocessor systems, to considerably increase the performance of digital servo drives and, above all, to increase the range of reachable performances. The technological leap with respect to the possibilities provided by analog-based technology is enormous since calibrations carried out with discrete components are eliminated to the full advantage of calibrations carried out exclusively via software. The drive’s internal software stores various sets of parameters and all operating functions, such as speed command from the analog input, torque control, position command, indexing, etc.
In addition, with digital servo drives, it is possible to obtain different levels of performance depending on the firmware version used – basic or advanced. The system architecture also includes the use of special modules to be inserted in the base of the drive capable of providing additional functionality. The latest generation of intelligent digital servo drive is, therefore, a process-oriented subsystem combined with a superior level of control.
Read Also: