FRL maintenance and efficiency tips for engineers
by Abdul Aziz Mondal Technology Published on: 13 January 2021 Last Updated on: 26 December 2024
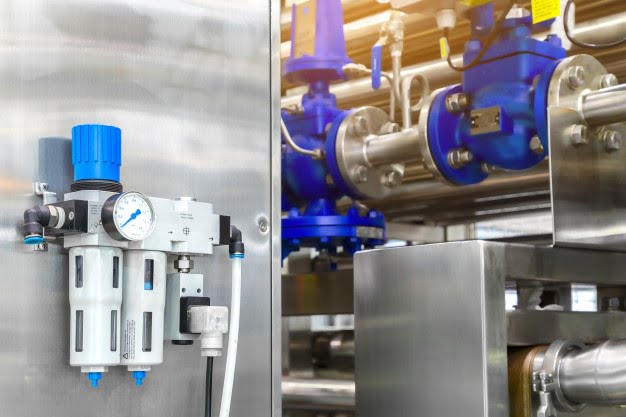
Over time, compressed air has become crucial to the process of automation, particularly in terms of optimizing performance and maintaining viable levels of energy efficiency.
Of course, compressed air also powers a wide range of machines and industrial equipment, each of which must be properly maintained in order to achieve peak performance and meet increasingly stringent safety guidelines.
This is where point-of-use filter regulator lubricator or FRL come into play, but how can you effectively utilize these to get the most from your various items of the equipment?
Why Does Equipment Powered by Air Compressors Fail?
Concepts such as automation and pneumatics rely on air compressors to function successfully, particularly in terms of safety and maintaining adequate fluid control.
However, such compressors and pneumatic cylinders are prone to various failures or breakdowns, one of the most prominent of which relates to side-load mounting.
In this instance, the side-load mounting aspect of pressurized cylinders means that the pivot mounts travel in an arc motion profile. This causes potential issues, due largely to misalignment, off-center loads, and imprecise tie-rod torque or long-stroke action.
This also explains why the critical assessment of a compressor’s efficiency is not when its position is stationary, but actually in motion. This is key maintenance consideration and one that can help you to get the most from your equipment.
Interestingly, compressors and equipment can also be contaminated internally from the air supply or the wider operational environment.
The most common types of contamination include oil, solids, and water, so it’s important to keep cylinders clean and clear on a regular basis.
How to Maintain Your Compressors and Make Them More Efficient
As you can imagine, FRL’s can play a pivotal role in maintaining safe and efficient machines. However, it’s important that you use them correctly if you’re to really get the most out of your equipment.
This type of approach can also reduce upfront costs while extending FRL service life and ensuring that equipment operates to specifications.
In terms of key maintenance issues, it’s important to note that the filter elements in a plant’s pneumatic system rarely get replaced at the intervals required to maintain peak performance. This will always lead to inefficient machine performance over time while causing instances of downtime and losses in productivity in the worst-case scenario.
When it comes to efficiency, you’ll also need to ensure that you and your team make the most of the advanced engineering tools at your disposal.
Certain software selection tools and product configurators enable engineers to specify FRLs and build the right combination of components, for example, which is crucial to deliver the requisite level of service.
Read Also: