The Art of Extraction – 5 Things to Know About Mineral Processing
by Abdul Aziz Mondal Community and Social Services 14 November 2018
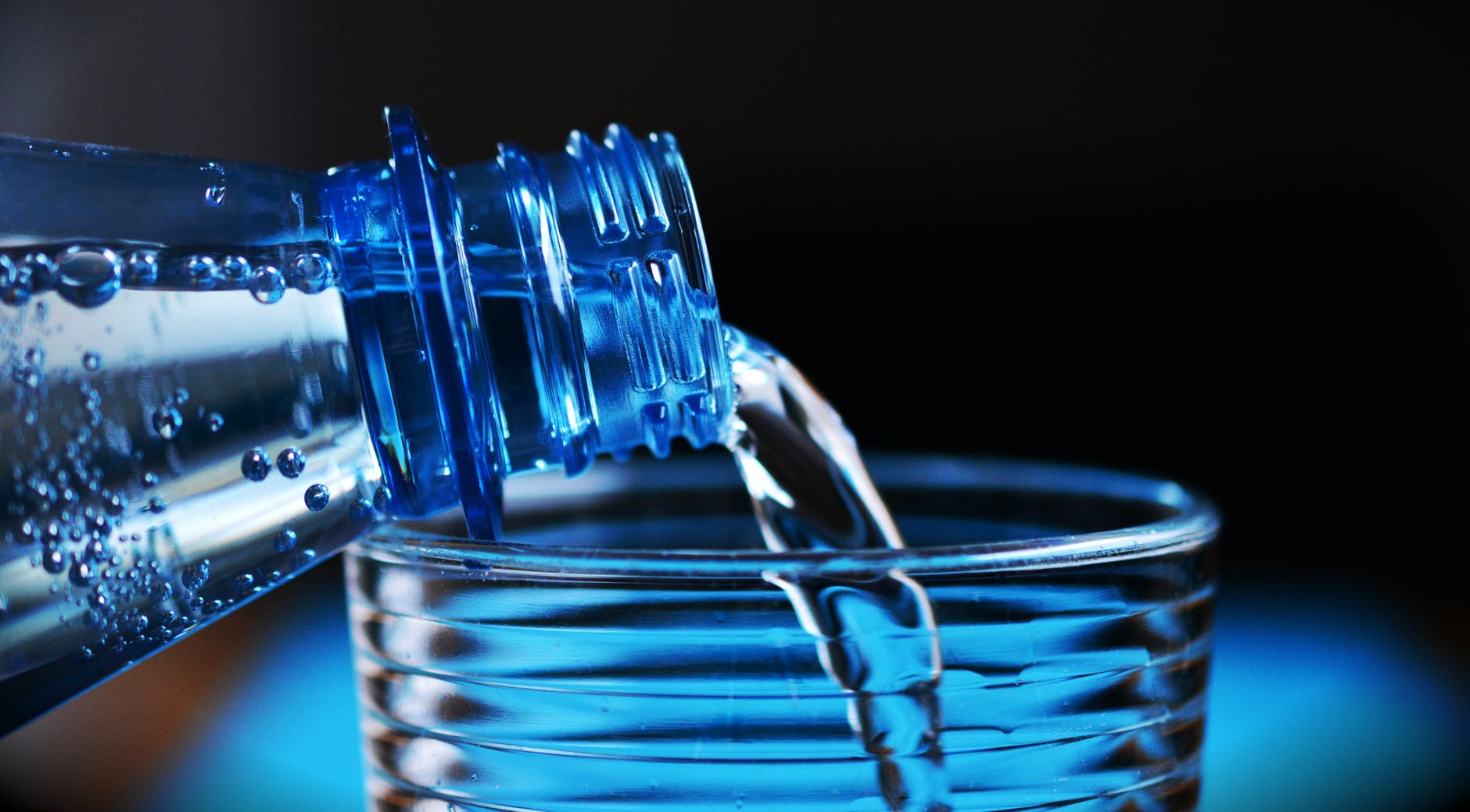
Mining is one of the biggest industries worldwide. From incredibly valuable metals such as gold and diamonds to sometimes underappreciated products such as copper and aluminum, the industry produces products man wouldn’t live without. And that’s before you consider the likes of salt, sand, oil, and gas that we depend on for daily life.
Which begs the question; do you even know how these products end up in your house? Do you understand how the likes of gold and silver are extracted and processed to make them the shiny metals we so much adore? Or, how salt from the ocean beds is processed until it ends up in the shops? We feel you should. So, here are five points to remember about the processing journey.
1. It begins with an ore:
A mineral ore is a term used to describe an aggregate of minerals from which valuable constituent minerals are extracted. Here’s a fun fact: most rocks contain metals or minerals. The difference is that ores contain a high enough concentration of the metals or minerals to justify mining. The other rocks that contain metals or minerals, but in low concentrations, are called gangue material and don’t justify mining.
2. An ore entering the processing plant is called run-of-mine:
Not all ores make it into the processing phase. Sometimes an ore that was thought to contain a high concentration of minerals might turn out to contain just a few traces of the mineral. However, if the ore is established to be potent enough to enter the processing phase, its name changes from ore to run-of-mine material. There are three types of run-of-mine materials; run-of-mine containing useful materials, run-of-mine containing useful minerals, and run-of-mine containing value bearing materials.
3. Mineral processing has not one, but two functions:
Most people think that mineral processing is just about extracting minerals from the ore. While that is correct, it’s not the only purpose of processing. The other purpose of processing is to separate the extracted materials into concentrates. A mineral concentrate is a ground ore that has had gangue (waste) removed from it, thus concentrating the metal component.
4. There are three key rules for mineral processing:
The first rule deals with mass conservation and says that the total flow of materials into the process plant must equal the total outflow. The second rule addresses the quality of concentrate products and says that it’s impossible to produce a concentrate containing just one metal. So, processers should work too hard chasing perfection. The third rule is almost similar to the second rule. It says that it’s impractical to recover all of the valuable minerals fed into the processing plant.
5. The single most important technique in mineral processing is – froth floatation!
A majority of people don’t know this. In fact, many people think that magnetic separation and perhaps sorting would rank higher. Well, that’s not the case. Beside mineral analysis, froth flotation is considered the most important stage of the processing journey. That’s because froth floatation has a unique ability to selectively separate minerals
Go Ahead, Learn More
At least now you know a few things about mineral processing. Feel free to dig deeper to better understand the process. It’s more fun that you’d imagine.
Read Also: